What are the typical energy savings of an all electric injection molding machine?
2024/08/19 By Topstar
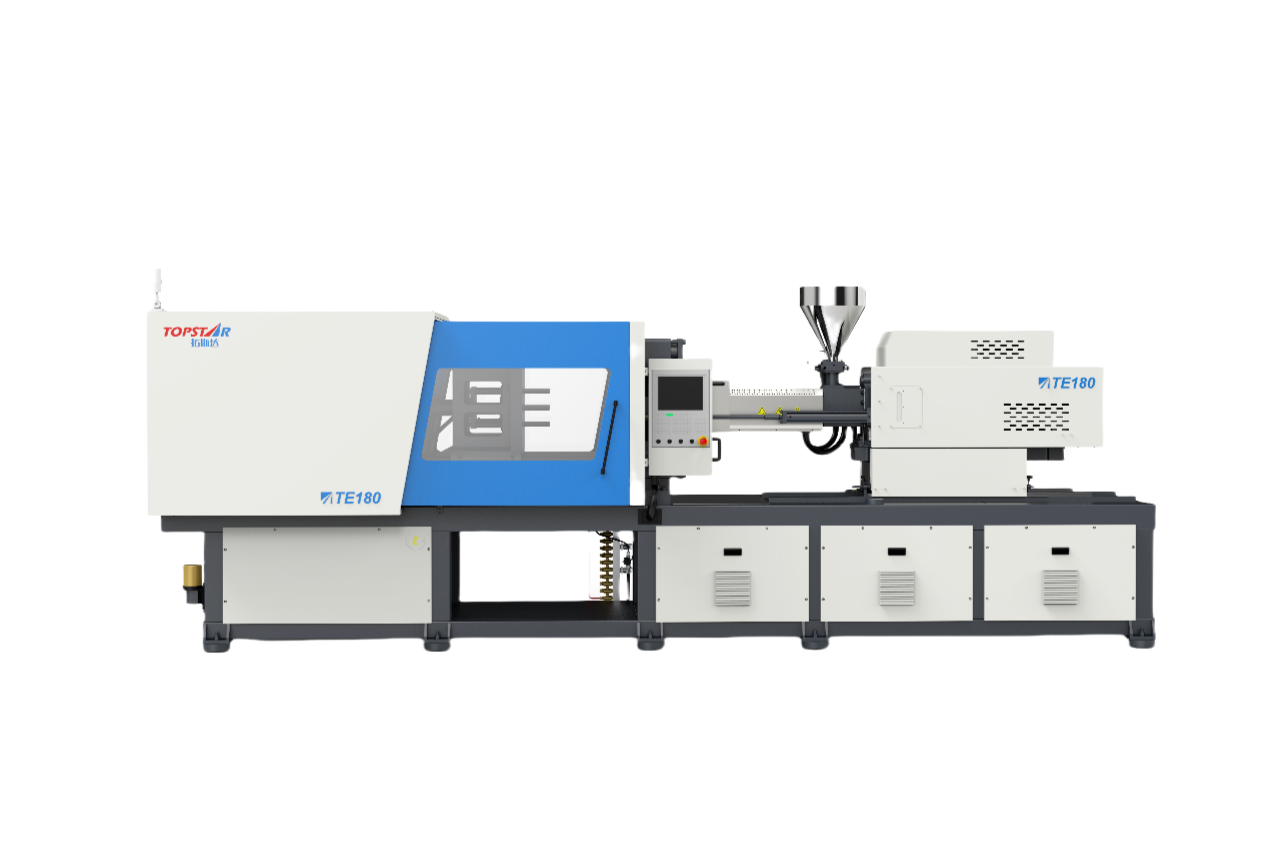
Throughout the injection molding production process, people are concerned about quality efficiency and energy conservation during the molding process. Rising energy costs and growing environmental concerns are prompting manufacturers to pursue more sustainable and cost-effective production methods. The all electric injection molding machine has the best energy-saving effect in injection molding, and they can save significantly more energy than hydraulic injection molding machines.
Energy consumption of all-electric injection molding machines
The key difference between all-electric injection molding machines and traditional hydraulic presses is the use of servo motors, which independently drive all major functions of the machine (such as injection, clamping and ejection) and perform precise control. Unlike hydraulic systems that continuously run pumps to maintain pressure, all-electric machines only consume energy when the motor runs, significantly reducing overall energy consumption. On this basis, Topstar’s TE ll series all-electric injection molding machines use the intelligent drive control mode to reduce the impact of communication delays on the high-speed operation of servo motors, realize real-time control of servo motors, improve the accuracy of position, speed and pressure control, and increase the response speed by 8-16 times.
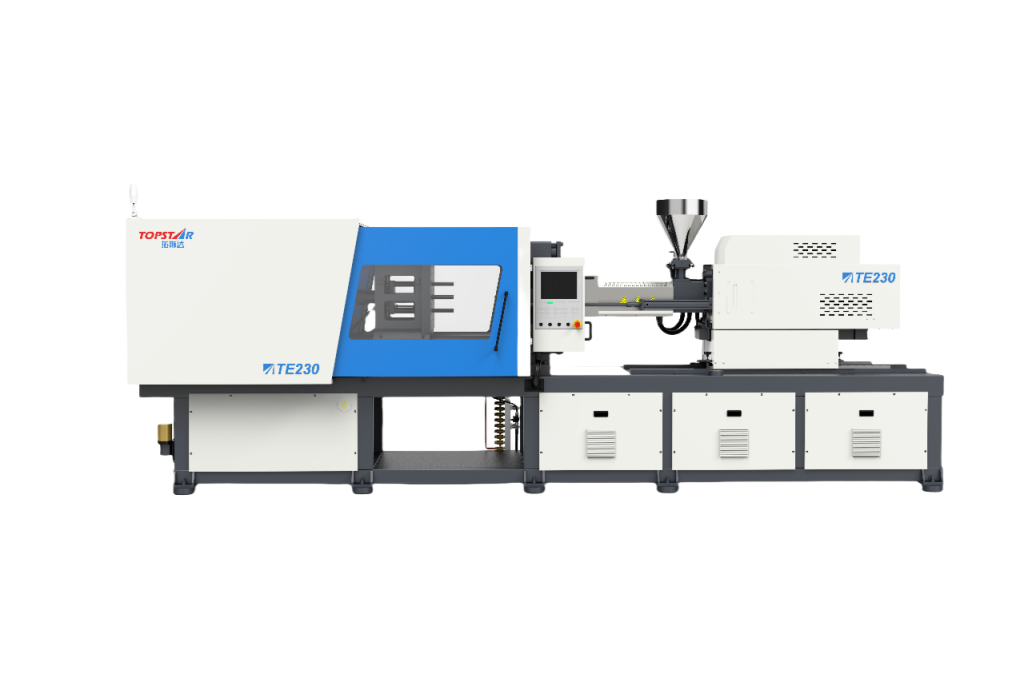
You can observe their energy-saving effects at all stages of the production process. For example, the system maintains pressure during the hold phase to ensure the mold is filled correctly. In contrast, a hydraulic press would continue running the pump, consuming much energy. They minimize energy consumption while using servo motors to control and maintain pressure precisely. This results in an energy consumption of 30% to 70% lower than that of a hydraulic press.
Energy savings in high-volume production
The energy savings of all-electric injection molding machines are more intuitive in high-volume production environments, such as home appliances, consumer goods, and the medical industry.
All-electric injection molding machines can operate with high precision and repeatability in high-volume production and consume less energy. Topstar’s TE ll series injection molding machines use an integrated injection seat in the injection unit, which makes control more precise under a highly rigid structure. Throughout the high-speed injection cycle, the servo motor can quickly and efficiently provide the required force, minimizing energy consumption during the injection phase. Once the part is molded, the motor can immediately reduce power consumption during the holding and cooling phases because these two phases require less force.
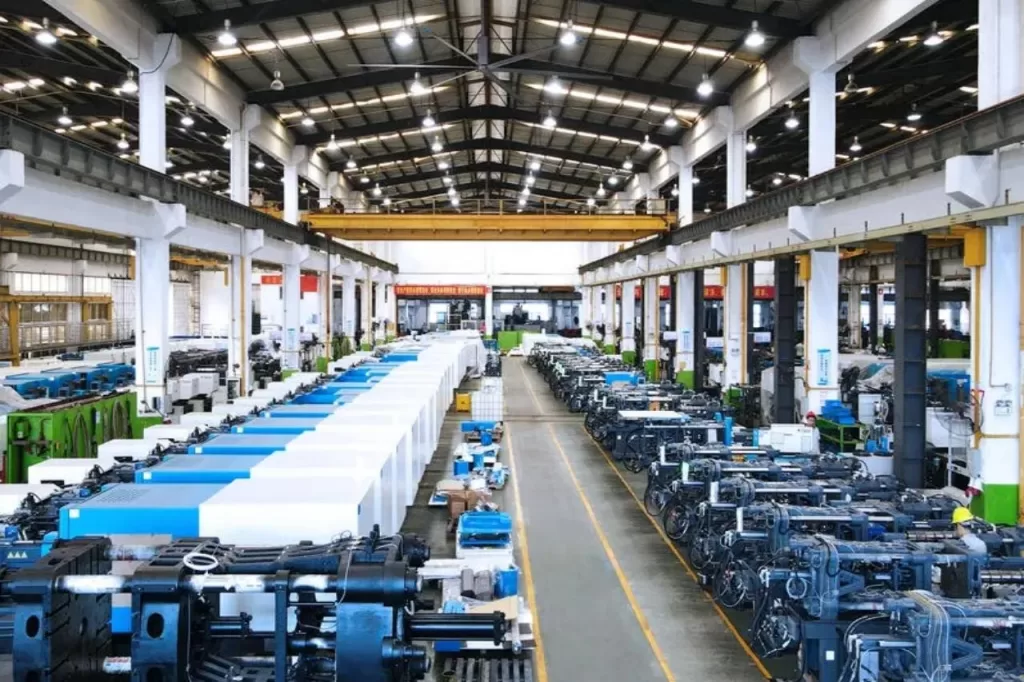
In addition, all-electric machines offer energy efficiency beyond just direct power consumption. These machines generally generate less heat during operation, reducing the need for auxiliary cooling systems. This further reduces overall energy usage and forms a more stable and controllable production environment.
The impact of all electric injection molding machine on energy costs
Energy costs have a direct impact on manufacturers’ profits. The power consumption of TE II series injection molding machines ranges from 3.8KWh to 17.9KWh, and the overall energy consumption is generally 30% to 70% lower than that of hydraulic presses. In addition to direct savings on electricity bills, all-electric injection molding machines have other cost-saving advantages. They can reduce the need for cooling systems and auxiliary equipment, reducing energy consumption and related maintenance and operating costs. Their overall mechanical design is simpler, and the non-contact tie rods used do not require lubrication, reducing the strain on the tie rods and reducing maintenance costs and downtime. The low damping brought by the linear guides makes the operation smoother. This stable performance and energy usage enable manufacturers to better control operating expenses, making planning and optimizing production easier.
Environmental benefits from energy saving
The energy-saving effect of all-electric injection molding machines can also bring certain environmental advantages, especially for industries with demanding production environments. They can reduce greenhouse gas emissions associated with energy use. Traditional hydraulic presses have high energy consumption and greater carbon emissions. All-electric machines can reduce energy use by up to 70%, helping to reduce the amount of carbon dioxide and other greenhouse gases emitted into the atmosphere. All-electric machines will not leak oil, etc., and their high net capacity is more suitable for use in industries such as medicine and optics.
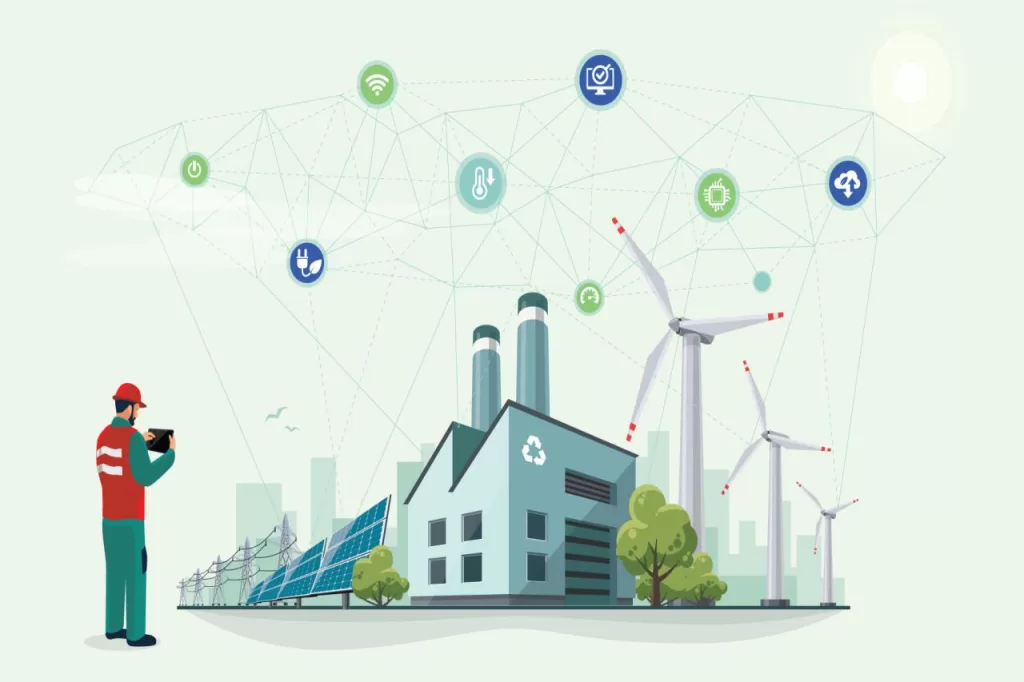
Leverage energy saving to bring you greater profits.
The advantages of all-electric injection molding machines are not limited to energy saving. They have precision, reliability and flexibility, making them ideal for mass production and precision manufacturing applications. As energy costs continue to rise, all-electric injection molding machines have been widely adopted in various industries. With our intelligent integrated injection molding machines and expert support, we can provide you with a comprehensive injection molding solution.
TRENDING POSTS
- What factors can cause delays in the injection molding process of plastic molding machine? 2024/08/19
- Exhibition Review| Topstar participates in InterPlas Thailand 2024 2024/08/19
- Star Case | Topstar helps Santong upgrade its intelligent plant 2024/08/19
- Topstar Special | National Science and Technology Workers Day 2024/08/19
HOT TOPIC
- .ervo motor-driven linear robots
- 1.0 guangdong topstar technology co. ltd
- 1.0 topstar china
- 1.0 topstar robot
- 11
- 2
- 21
- 23
- 3 axis robot
- 3 axis robots
- 3 in 1 Compact Dehumidifying Dryer
- 3-axis robot
- 3-axis robots
- 39
- 41
- 5-axis CNC machine
- 62
- accuracy
- Air Chillers
- all electric injection molding machine
- all electric injection molding machines
- All-electric injection molding machines
- and overall production quality. Therefore
- AP-RubberPlas
- automated injection molding machine
- Automation changed engineering
- automation of injection molding robots
- auxiliary machine
- Bench Injection Molding Machine
- Cabinet dryer manufacturers
- Cabinet dryers
- chiller
- CNC Drilling Machine
- CNC Drilling Machines
- cnc engraving machine manufacturer
- cnc laser cutting machine manufacturer
- CNC machine
- CNC Machine Center
- CNC Machine for Sale
- CNC Machine Manufacturing
- CNC Machine Tool
- CNC machine tool product
- CNC Machining Center
- CNC wood carving machine
- Cooling system
- Cross-Walking Single Axis Servo Cylinder Robot
- Cross-Walking Single-Axis Servo Cylinder Robot
- Cross-Walking Three-Axis/Five-Axis Servo Driven Robot
- cross-walking three-axis/five-axis servo-driven robot
- Dehumidifier Dryer
- Dehumidifying Dryer
- delta parallel robot
- Desktop Injection Molding Machine
- Desktop injection molding machines
- Desktop Molding Machine
- desktop plastic injection machine
- Desktop Plastic Injection Molding Machine
- direct clamp injection molding machine
- Direct clamp injection molding machines
- Dosing & mixing system
- Drilling Centers
- Drying and dehumidification system
- drying and dehumidifying equipment
- Drying and Dehumidifying System
- drying system
- effective and efficient. Cabinet dryers are also used in other industries where large quantities of material need to be dried
- efficient injection molding machine
- elbow hydraulic injection molding machines
- electric injection molding machine
- electric injection molding machines
- energy-efficient injection molding robot
- energy-saving injection molding machine
- etc. Among injection molding robots
- exhibition
- features of CNC machine
- Feeding And Conveying System
- Five Axis Machine Center
- Fully automatic injection molding machine
- Gathering Topstar
- giant injection molding machine
- GMU-600 5-Axis Machining Center
- Granulating & Recycling System
- Heavy duty injection molding machine
- High-precision electric molding machines
- high-precision plastic molding machines
- high-speed all electric injection molding machine
- Honeycomb rotor dehumidifier
- horizontal injection molding machine
- Horizontal Injection Molding Machines
- Horizontal Injection Moulding Machine
- Horizontal Mixer manufacturer
- How The CNC Machine Works
- hybrid injection molding machine
- hydraulic injection molding machine
- Hydraulic Injection Molding Machines
- in this article
- Industrial robot
- Industrial Robot Chinese brand
- industrial robot parts
- industrial robot supplier
- Industrial robots
- Industry Chain
- Injection Manipulator
- injection manipulator robot
- injection mold machines
- Injection molding
- Injection molding automation
- Injection Molding Automation Solution
- injection molding dryer
- Injection molding equipment
- injection molding hopper dryer
- Injection molding machine
- injection molding machine brand
- Injection Molding Machine Factory
- Injection Molding Machine Manufacture
- Injection molding machine manufacturer
- injection molding machine manufacturers
- Injection molding machine procurement
- injection molding machine robotic arm
- injection molding machine with a robot
- Injection molding machines
- injection molding material dehumidifying
- injection molding plant
- Injection Molding Robot
- injection molding robot arm
- Injection molding robot automation
- Injection molding robotic arm
- injection molding robots
- Injection moulding machine
- injection moulding machines
- Injection Moulding Robots
- Injection Robot
- Injection robot arm
- Injection robot manufacturer
- Injection robot wholesale
- injection robots
- intelligent injection molding machines
- Introducing Injection Robot
- It is the best choice for drying large quantities of material at once. Cabinetmakers use these machines because they are fast
- large injection molding machine
- large injection molding machines
- Learn what industrial automation and robotics is
- linear robot
- linear robots
- low speed sound-proof granulator
- machine plastic molding
- make sure to add some! Improvements (2) Keyphrase in introduction: Your keyphrase or its synonyms appear in the first paragraph of the copy
- manipulator machine
- manufacturing
- medical grade injection molding machines
- medical injection molding machine
- medical injection molding machines
- micro injection molding machine
- middle speed granulator
- Mini CNC machine manufacturers.
- Mold Temperature Control System
- mold temperature controller
- mold temperature controllers
- molding material Dehumidifying System
- mould temperature control system
- mould temperature controller
- mould temperature controllers
- New electric injection molding machine
- nitrogen dryer manufacturer
- nitrogen dryer system manufacturer
- Oil type mold temperature controller
- Oil type mold temperature controllers
- open day
- Outbound links: No outbound links appear in this page. Add some! Images: No images appear on this page. Add some! Internal links: No internal links appear in this page
- PET Preform injection molding
- phone case maker machine
- phone case making machine
- plastic bottle making machine
- plastic bottle manufacturing
- plastic bucket making machine
- plastic bucket manufacturing
- Plastic chair making machine
- plastic forming equipment
- plastic hopper dryer
- plastic injection machine
- plastic injection machines
- plastic injection molding
- Plastic injection molding equipment
- Plastic injection molding machine
- Plastic Injection Molding Machines
- plastic injection moulding machine
- plastic injection moulding machines
- plastic injection robot
- Plastic Molding machine
- Plastic Molding Machines
- plastic molding press
- plastic moulding machine
- plastic phone case making machine
- plastic-molding machine
- powerful granulator
- Powerful Type Sound-Proof Granulator
- precision injection molding
- precision injection molding machines
- production of plastic seats
- pure water mould temperature controller
- Robot injection molding
- robot injection molding machine
- robot manufacturing companies
- Robotic arm for injection molding machine
- robotic injection molding machines
- robotics in injection molding
- SCARA robot
- SCARA robots
- Service-oriented manufacturing
- Servo Cylinder Robot
- servo driven robot
- Servo Driven Robots
- servo injection robots
- servo motor-driven linear robots
- servo-driven 3-axis robot
- Servo-Driven Robot
- Setup of injection machine
- Silicone Injection Molding Machine
- six-axis industrial robot
- Stainless Hopper Dryer
- Stainless Hopper Dryers
- star club
- swing arm robot
- take-out robots
- the choice between servo-driven robots and hydraulic robots will have a certain impact on efficiency
- the most popular injection molding machine
- the type of injection molding robot
- toggle clamp injection molding machine
- Toggle Hydraulic Injection Molding Machines
- toggle injection molding machine
- Top 10 brands of injection robots
- Topstar
- Topstar Engineering
- Topstar Industrial Robots
- Topstar injection molding intelligent
- Topstar Scara Robots
- Useful Injection molding machine
- Vertical machining centers
- volumetric type blender
- water chiller
- water chillers
- water distributor
- water type mold temperature controller
- Water Type MoldTemperature Controller
- Water-Type Mould Temperature Controllers
- We often face choices when performing injection molding. We will choose the type of injection molding machine
- wholesale of injection molding machines
- x carve CNC
- 热门查询 点击次数 展示 排名 topstar