What safety features can you look for in a plastic injection molding machine?
2024/06/03 By Topstar
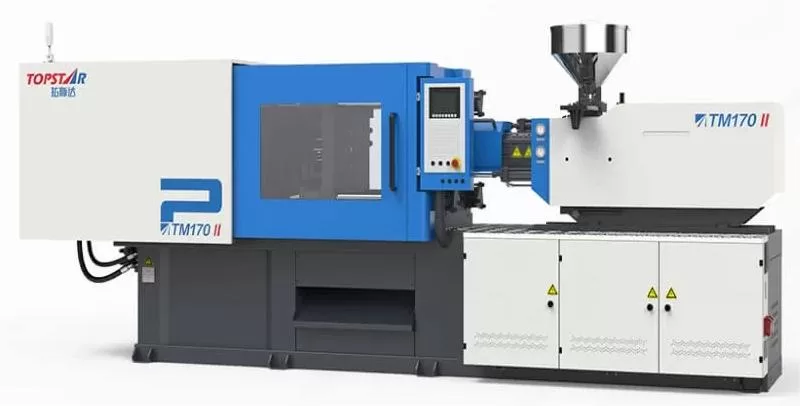
Industry 4.0 has brought a lot of convenience to large-scale manufacturing, reducing the number of people working in the workshop, but even so, some operators will still be retained. Safety is especially important when operating machinery such as plastic injection molding machine. These machines are large tools for making various plastic products, but they can be very dangerous to the human body if used improperly. This guide will explore the various safety features added to Tosda’s early plastic injection molding machine. These safety features are also one of the factors that many plastic manufacturers will consider when purchasing.
Safety interlocks of safety functions of plastic injection molding machines
The most basic safety function in plastic injection molding machines is safety interlocks. These interlocks are designed to prevent the machine from running when certain conditions are not met, such as when the safety guard is open, or the mold is not properly fixed. By requiring these conditions to be met before the machine can run, safety interlocks help reduce the risk of accidents and injuries.
It can prevent entry into the danger zone of the injection molding machine while it is running. It is equivalent to a physical barrier or electronic control mechanism that can limit access to the machine’s moving parts. Our plastic injection molding machines use a combination of mechanical and electronic interlocks to ensure comprehensive safety protection. Mechanical interlocks include physical barriers, such as doors, gates, or guards, that automatically close and lock when the machine is in operation. Electronic interlocks utilize sensors, switches, and PLCs to detect unsafe conditions.
Emergency Stop Button
Another important safety feature is the emergency stop button, also known as the e-stop button. It is a conspicuous and easily accessible control device located on the control panel of the plastic injection molding machine. Its main function is to immediately stop all machine operations in the event of an emergency or dangerous situation. When activated, the E-stop triggers a safety shutdown sequence that removes power from the machine, stops all moving parts, and prevents further processing of materials. Their main advantage is the ability to respond immediately to a variety of potential dangers and emergencies, whether it is a mechanical failure, electrical failure, material jam, etc., pressing the emergency stop button ensures that the machine stops running in time to reduce the risk of accidents, injuries, and equipment damage.
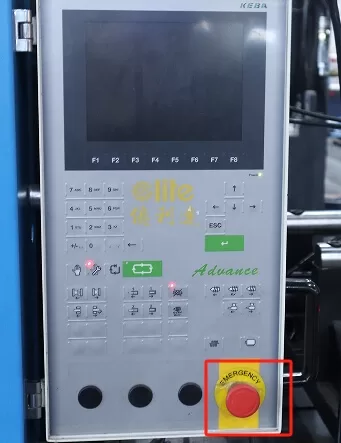
Safety Guards and Barriers
Safety guards and barriers are physical barriers that establish a physical barrier between the operator and parts of the plastic injection molding machine, such as the mold clamping unit, injection unit, and ejection system. Their main function is to prevent inadvertent contact with dangerous areas and reduce the risk of accidents, injuries, and equipment damage. Safety guards and barriers surround and protect these areas, ensuring operators can work safely.Manufacturers typically make these physical barriers from durable materials, designing them to prevent contact with moving parts and hot surfaces during operation.
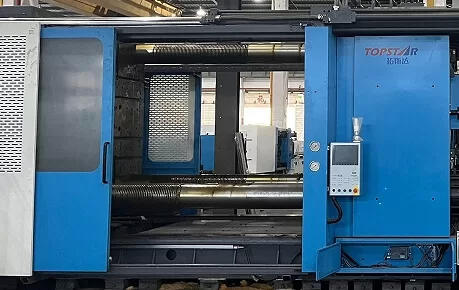
Overpressure and overtemperature alarms
Manufacturers equip many plastic injection molding machines with overpressure and overtemperature alarms to enhance safety further. These alarms alert operators when pressure or temperature levels exceed safe limits, allowing them to take corrective action before dangerous conditions occur. Overpressure and overheating alarms monitor pressure and temperature levels within the hydraulic system, barrel, and mold of plastic injection molding machines.
Their main function is to detect abnormal conditions, such as excessive pressure or temperature increases, which may indicate a potential malfunction, leak, or system failure. When triggered, these alarms sound an audible or visual alert, notifying the operator so they can take corrective action and prevent the problem from escalating further.
Integrated Safety PLC
Plastic injection molding machines also integrate PLCs with safety features that provide comprehensive safety monitoring and control capabilities. These PLCs can oversee a variety of safety features, such as interlocks, emergency stops, and alarm systems, and can automatically implement safety protocols based on detected risks. An integrated safety PLC is a central control system that manages and monitors safety features throughout the injection molding machine. By integrating safety features into a single, centralized platform, the PLC ensures consistent and reliable safety features for all aspects of machine operation.
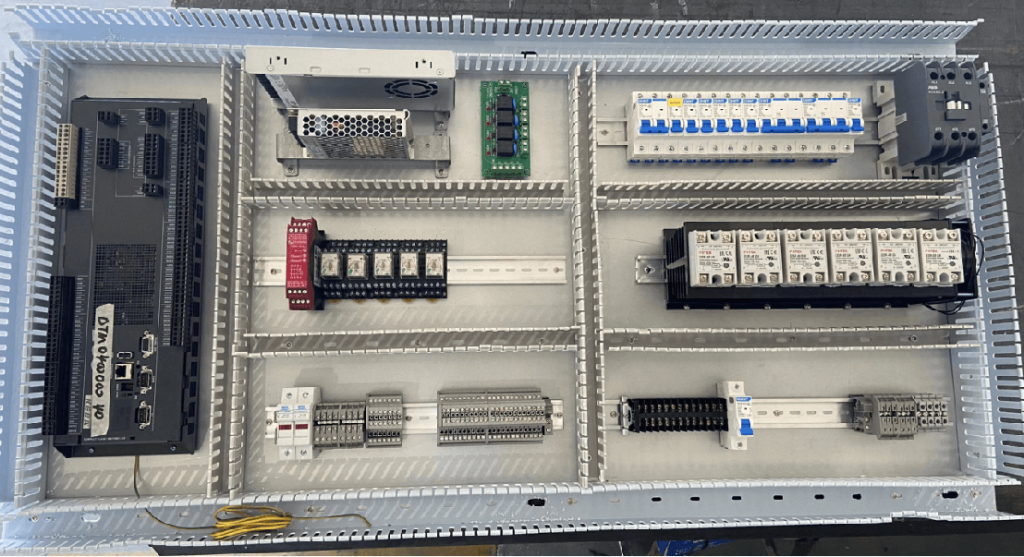
Make Your Plastic Injection Molding Machine and Operator Safer
Plastic injection molding machines are essential machines for plastic manufacturers to produce parts, and they also pose certain risks to operators if used improperly. Combining various safety features enables manufacturers to mitigate these risks and promote a safe working environment.
TRENDING POSTS
- What factors can cause delays in the injection molding process of plastic molding machine? 2024/06/03
- Exhibition Review| Topstar participates in InterPlas Thailand 2024 2024/06/03
- Star Case | Topstar helps Santong upgrade its intelligent plant 2024/06/03
- Topstar Special | National Science and Technology Workers Day 2024/06/03
HOT TOPIC
- .ervo motor-driven linear robots
- 3 axis robot
- 3 axis robots
- 3 in 1 Compact Dehumidifying Dryer
- 3-axis robot
- 3-axis robots
- 5-axis CNC machine
- accuracy
- Air Chillers
- all electric injection molding machine
- all electric injection molding machines
- All-electric injection molding machines
- and overall production quality. Therefore
- AP-RubberPlas
- automated injection molding machine
- Automation changed engineering
- automation of injection molding robots
- auxiliary machine
- Bench Injection Molding Machine
- Cabinet dryer manufacturers
- Cabinet dryers
- chiller
- CNC Drilling Machine
- CNC Drilling Machines
- cnc engraving machine manufacturer
- cnc laser cutting machine manufacturer
- CNC machine
- CNC Machine Center
- CNC Machine for Sale
- CNC Machine Manufacturing
- CNC Machine Tool
- CNC machine tool product
- CNC Machining Center
- CNC wood carving machine
- Cooling system
- Cross-Walking Single Axis Servo Cylinder Robot
- Cross-Walking Single-Axis Servo Cylinder Robot
- Cross-Walking Three-Axis/Five-Axis Servo Driven Robot
- cross-walking three-axis/five-axis servo-driven robot
- Dehumidifier Dryer
- Dehumidifying Dryer
- delta parallel robot
- Desktop Injection Molding Machine
- Desktop injection molding machines
- Desktop Molding Machine
- desktop plastic injection machine
- Desktop Plastic Injection Molding Machine
- direct clamp injection molding machine
- Direct clamp injection molding machines
- Dosing & mixing system
- Drilling Centers
- Drying and dehumidification system
- drying and dehumidifying equipment
- Drying and Dehumidifying System
- drying system
- effective and efficient. Cabinet dryers are also used in other industries where large quantities of material need to be dried
- efficient injection molding machine
- elbow hydraulic injection molding machines
- electric injection molding machine
- electric injection molding machines
- energy-efficient injection molding robot
- energy-saving injection molding machine
- etc. Among injection molding robots
- exhibition
- features of CNC machine
- Feeding And Conveying System
- Five Axis Machine Center
- Fully automatic injection molding machine
- Gathering Topstar
- giant injection molding machine
- GMU-600 5-Axis Machining Center
- Granulating & Recycling System
- Heavy duty injection molding machine
- High-precision electric molding machines
- high-precision plastic molding machines
- high-speed all electric injection molding machine
- Honeycomb rotor dehumidifier
- horizontal injection molding machine
- Horizontal Injection Molding Machines
- Horizontal Injection Moulding Machine
- Horizontal Mixer manufacturer
- How The CNC Machine Works
- hybrid injection molding machine
- hydraulic injection molding machine
- Hydraulic Injection Molding Machines
- in this article
- Industrial robot
- Industrial Robot Chinese brand
- industrial robot parts
- industrial robot supplier
- Industrial robots
- Industry Chain
- Injection Manipulator
- injection manipulator robot
- injection mold machines
- Injection molding
- Injection molding automation
- Injection Molding Automation Solution
- injection molding dryer
- Injection molding equipment
- injection molding hopper dryer
- Injection molding machine
- injection molding machine brand
- Injection Molding Machine Factory
- Injection Molding Machine Manufacture
- Injection molding machine manufacturer
- injection molding machine manufacturers
- Injection molding machine procurement
- injection molding machine robotic arm
- injection molding machine with a robot
- Injection molding machines
- injection molding material dehumidifying
- injection molding plant
- Injection Molding Robot
- injection molding robot arm
- Injection molding robot automation
- Injection molding robotic arm
- injection molding robots
- Injection moulding machine
- Injection Moulding Robots
- Injection Robot
- Injection robot arm
- Injection robot manufacturer
- Injection robot wholesale
- injection robots
- intelligent injection molding machines
- Introducing Injection Robot
- It is the best choice for drying large quantities of material at once. Cabinetmakers use these machines because they are fast
- large injection molding machine
- Learn what industrial automation and robotics is
- linear robot
- linear robots
- low speed sound-proof granulator
- machine plastic molding
- make sure to add some! Improvements (2) Keyphrase in introduction: Your keyphrase or its synonyms appear in the first paragraph of the copy
- manipulator machine
- manufacturing
- medical grade injection molding machines
- medical injection molding machine
- medical injection molding machines
- micro injection molding machine
- middle speed granulator
- Mini CNC machine manufacturers.
- Mold Temperature Control System
- mold temperature controller
- mold temperature controllers
- molding material Dehumidifying System
- mould temperature control system
- mould temperature controller
- mould temperature controllers
- New electric injection molding machine
- nitrogen dryer manufacturer
- nitrogen dryer system manufacturer
- Oil type mold temperature controller
- Oil type mold temperature controllers
- open day
- Outbound links: No outbound links appear in this page. Add some! Images: No images appear on this page. Add some! Internal links: No internal links appear in this page
- PET Preform injection molding
- phone case maker machine
- phone case making machine
- plastic bottle making machine
- plastic bottle manufacturing
- plastic bucket making machine
- plastic bucket manufacturing
- Plastic chair making machine
- plastic forming equipment
- plastic hopper dryer
- plastic injection machine
- plastic injection machines
- plastic injection molding
- Plastic injection molding equipment
- Plastic injection molding machine
- Plastic Injection Molding Machines
- plastic injection moulding machine
- plastic injection robot
- Plastic Molding machine
- Plastic Molding Machines
- plastic molding press
- plastic moulding machine
- plastic phone case making machine
- plastic-molding machine
- powerful granulator
- Powerful Type Sound-Proof Granulator
- precision injection molding
- precision injection molding machines
- production of plastic seats
- pure water mould temperature controller
- Robot injection molding
- robot injection molding machine
- robot manufacturing companies
- Robotic arm for injection molding machine
- robotic injection molding machines
- robotics in injection molding
- SCARA robot
- SCARA robots
- Service-oriented manufacturing
- Servo Cylinder Robot
- servo driven robot
- Servo Driven Robots
- servo injection robots
- servo motor-driven linear robots
- servo-driven 3-axis robot
- Servo-Driven Robot
- Setup of injection machine
- Silicone Injection Molding Machine
- six-axis industrial robot
- Stainless Hopper Dryer
- Stainless Hopper Dryers
- star club
- swing arm robot
- take-out robots
- the choice between servo-driven robots and hydraulic robots will have a certain impact on efficiency
- the most popular injection molding machine
- the type of injection molding robot
- toggle clamp injection molding machine
- Toggle Hydraulic Injection Molding Machines
- toggle injection molding machine
- Top 10 brands of injection robots
- Topstar
- Topstar Engineering
- Topstar Industrial Robots
- Topstar injection molding intelligent
- Topstar Scara Robots
- Useful Injection molding machine
- Vertical machining centers
- volumetric type blender
- water chiller
- water chillers
- water distributor
- water type mold temperature controller
- Water Type MoldTemperature Controller
- Water-Type Mould Temperature Controllers
- We often face choices when performing injection molding. We will choose the type of injection molding machine
- wholesale of injection molding machines
- x carve CNC