What is the service life of an injection molding robot arm?
2024/05/03 By Topstar
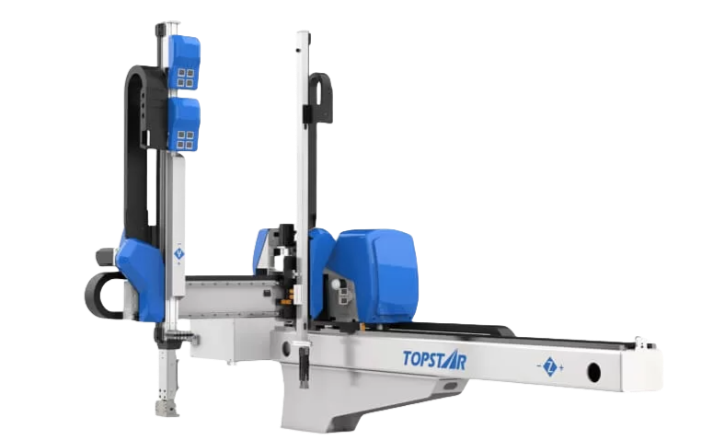
The injection molding robot arm is an auxiliary device that can help the injection molding machine grab materials during injection molding. It is usually located on top of the machine. These robotic arms can perform precise and repetitive movements, handling parts quickly and accurately. Therefore, many manufacturers will ask about their service life when purchasing, which can also affect the future layout of their entire production line. So, in this article, we will help you to understand its service life and the factors that affect it.
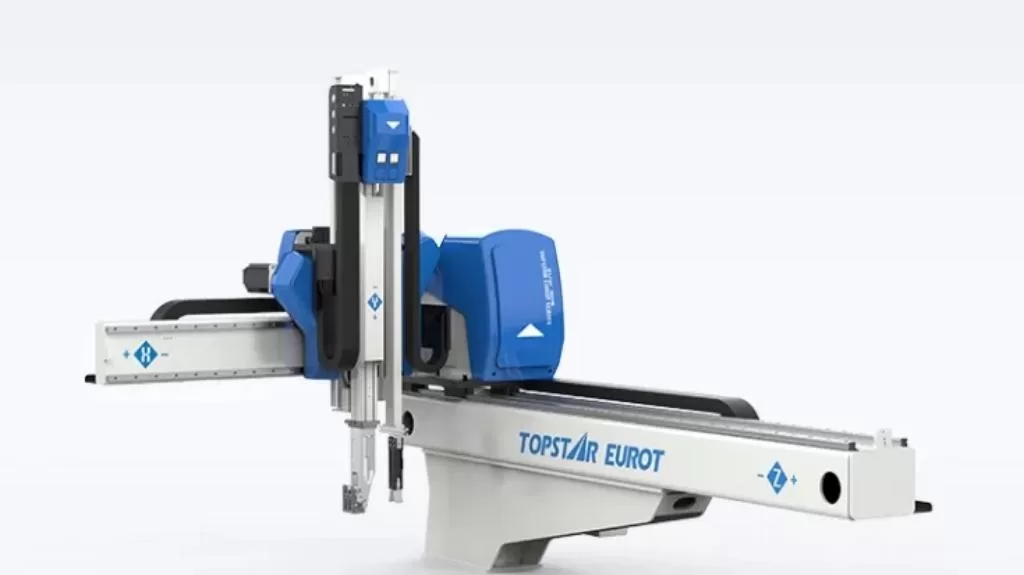
Service life of injection molding robot arm
Topstar’s injection molding robot arms‘ typical service life should be 8 to 15 years. The robotic arm will be made of lightweight aluminum alloy to withstand the rigors of continuous industrial use. The DC bus technology used saves 10% of the overall energy. It adds automatic servo OFF so that the motor can stop powering when the servo is on standby. It reduces the power cost by 10%, avoiding too much energy consumption during operation and reducing the service life.
Quality of injection molded robotic arm components and structures
The quality of the parts and structure of the injection molded robotic arm fundamentally determines its service life. Structural components, joints, and shells are usually made of high-grade materials such as high-quality aluminum alloy. These materials were chosen for their sufficient strength, wear resistance, and ability to withstand the mechanical stresses of the injection molding machine. Rack-and-pinion meshing transmission is used at the front and rear to achieve higher positioning accuracy. This precision engineering ensures smooth movement and reduces friction at the joint interface, reducing the risk of premature wear.
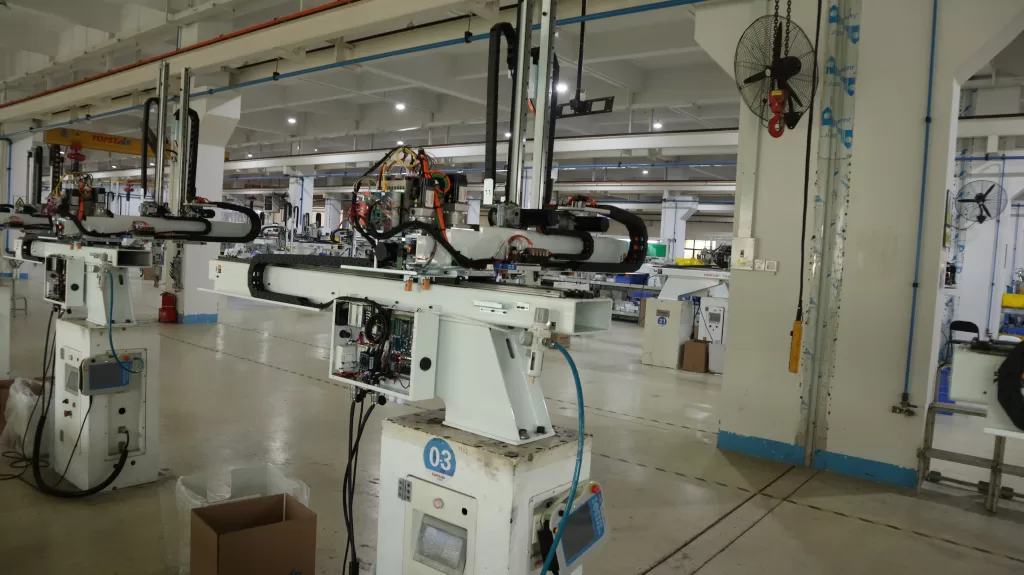
Operation frequency and workload
The service life of an injection molding robotic arm is also closely related to its operating frequency and workload. High-frequency operations usually lead to faster wear of mechanical components such as joints, gears, and bearings. Workload refers to the force or weight the robotic arm handles during operation. This also includes the forces exerted on the arm during movement. Generally, the structure determines the applicable load range of the injection molding robot arm. Exceeding the standard load weight will accelerate the fatigue of the metal structure and the wear of precision components such as servo motors and hydraulic systems, thereby shortening the overall service life.
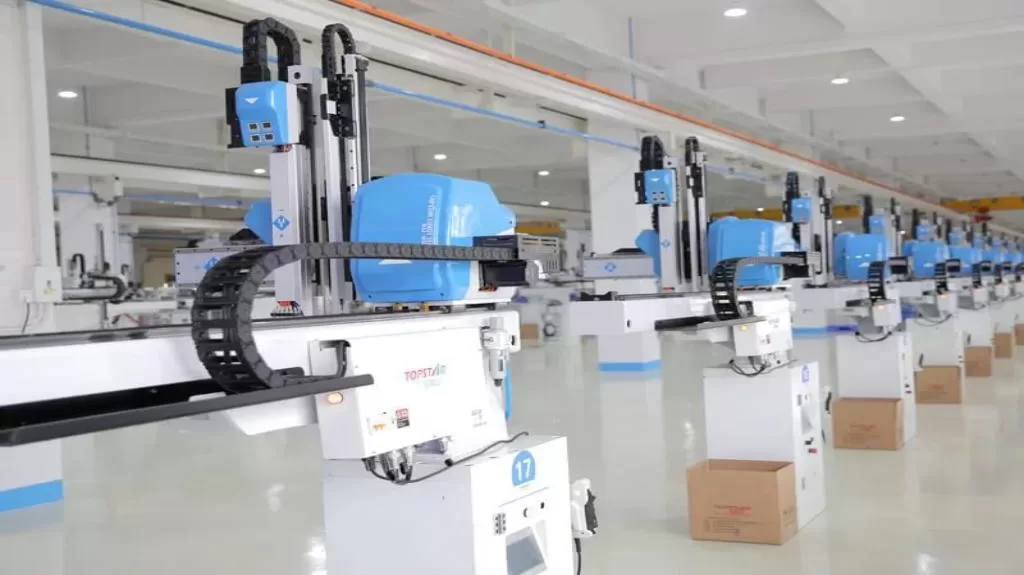
Maintenance and preventive care
The relationship between maintenance and preventive care and the service life of the injection molding robot is the basis for ensuring optimal performance and service life. During daily operations, routine inspections, lubrication of moving parts, and replacement of worn parts are required. Maintenance work can minimize the wear and tear of critical components. This proactive approach maintains the structural integrity of the robotic arm, preventing premature failure and extending its service life. Proper lubrication reduces friction, allowing for smoother movement and less stress on mechanical components. Regular inspections and proactive component replacement reduce the likelihood of unexpected failures, ensuring continuous operation and production continuity.
Environmental conditions
Environmental factors will also indirectly affect the durability and function of the robotic arm. Wear will be accelerated if exposed to adverse temperature conditions, leading to premature failure. High temperatures can cause the injection molding robot’s motor and drive system to overheat, causing thermal stress on electronic circuits and causing control system failure. Temperatures too low can cause lubricants and hydraulic fluids to harden, reducing their effectiveness and increasing friction in moving parts. Humidity is also an important environmental factor. High humidity can promote corrosion of metal components and condensation in electronic systems, which can lead to short circuits or component oxidation. Therefore, we need to control the temperature well in the injection molding workshop, and a dehumidifier can be added to alleviate these problems.
Ultimately
The service life of injection molding robot arms typically ranges from 8 to 15 years. Factors affecting their service life include component quality, frequency of operation, and maintenance methods. In addition to choosing high-quality injection molding robot arms, you can protect them and extend their service life by implementing proper maintenance.
TRENDING POSTS
- What factors can cause delays in the injection molding process of plastic molding machine? 2024/05/03
- Exhibition Review| Topstar participates in InterPlas Thailand 2024 2024/05/03
- Star Case | Topstar helps Santong upgrade its intelligent plant 2024/05/03
- Topstar Special | National Science and Technology Workers Day 2024/05/03
HOT TOPIC
- .ervo motor-driven linear robots
- 3 axis robot
- 3 axis robots
- 3 in 1 Compact Dehumidifying Dryer
- 3-axis robot
- 3-axis robots
- 5-axis CNC machine
- accuracy
- Air Chillers
- all electric injection molding machine
- all electric injection molding machines
- All-electric injection molding machines
- and overall production quality. Therefore
- AP-RubberPlas
- automated injection molding machine
- Automation changed engineering
- automation of injection molding robots
- auxiliary machine
- Bench Injection Molding Machine
- Cabinet dryer manufacturers
- Cabinet dryers
- chiller
- CNC Drilling Machine
- CNC Drilling Machines
- cnc engraving machine manufacturer
- cnc laser cutting machine manufacturer
- CNC machine
- CNC Machine Center
- CNC Machine for Sale
- CNC Machine Manufacturing
- CNC Machine Tool
- CNC machine tool product
- CNC Machining Center
- CNC wood carving machine
- Cooling system
- Cross-Walking Single Axis Servo Cylinder Robot
- Cross-Walking Single-Axis Servo Cylinder Robot
- Cross-Walking Three-Axis/Five-Axis Servo Driven Robot
- cross-walking three-axis/five-axis servo-driven robot
- Dehumidifier Dryer
- Dehumidifying Dryer
- delta parallel robot
- Desktop Injection Molding Machine
- Desktop injection molding machines
- Desktop Molding Machine
- desktop plastic injection machine
- Desktop Plastic Injection Molding Machine
- direct clamp injection molding machine
- Direct clamp injection molding machines
- Dosing & mixing system
- Drilling Centers
- Drying and dehumidification system
- drying and dehumidifying equipment
- Drying and Dehumidifying System
- drying system
- effective and efficient. Cabinet dryers are also used in other industries where large quantities of material need to be dried
- efficient injection molding machine
- elbow hydraulic injection molding machines
- electric injection molding machine
- electric injection molding machines
- energy-efficient injection molding robot
- energy-saving injection molding machine
- etc. Among injection molding robots
- exhibition
- features of CNC machine
- Feeding And Conveying System
- Five Axis Machine Center
- Fully automatic injection molding machine
- Gathering Topstar
- giant injection molding machine
- GMU-600 5-Axis Machining Center
- Granulating & Recycling System
- Heavy duty injection molding machine
- High-precision electric molding machines
- high-precision plastic molding machines
- high-speed all electric injection molding machine
- Honeycomb rotor dehumidifier
- horizontal injection molding machine
- Horizontal Injection Molding Machines
- Horizontal Injection Moulding Machine
- Horizontal Mixer manufacturer
- How The CNC Machine Works
- hybrid injection molding machine
- hydraulic injection molding machine
- Hydraulic Injection Molding Machines
- in this article
- Industrial robot
- Industrial Robot Chinese brand
- industrial robot parts
- industrial robot supplier
- Industrial robots
- Industry Chain
- Injection Manipulator
- injection manipulator robot
- injection mold machines
- Injection molding
- Injection molding automation
- Injection Molding Automation Solution
- injection molding dryer
- Injection molding equipment
- injection molding hopper dryer
- Injection molding machine
- injection molding machine brand
- Injection Molding Machine Factory
- Injection Molding Machine Manufacture
- Injection molding machine manufacturer
- injection molding machine manufacturers
- Injection molding machine procurement
- injection molding machine robotic arm
- injection molding machine with a robot
- Injection molding machines
- injection molding material dehumidifying
- injection molding plant
- Injection Molding Robot
- injection molding robot arm
- Injection molding robot automation
- Injection molding robotic arm
- injection molding robots
- Injection moulding machine
- Injection Moulding Robots
- Injection Robot
- Injection robot arm
- Injection robot manufacturer
- Injection robot wholesale
- injection robots
- intelligent injection molding machines
- Introducing Injection Robot
- It is the best choice for drying large quantities of material at once. Cabinetmakers use these machines because they are fast
- large injection molding machine
- Learn what industrial automation and robotics is
- linear robot
- linear robots
- low speed sound-proof granulator
- machine plastic molding
- make sure to add some! Improvements (2) Keyphrase in introduction: Your keyphrase or its synonyms appear in the first paragraph of the copy
- manipulator machine
- manufacturing
- medical grade injection molding machines
- medical injection molding machine
- medical injection molding machines
- micro injection molding machine
- middle speed granulator
- Mini CNC machine manufacturers.
- Mold Temperature Control System
- mold temperature controller
- mold temperature controllers
- molding material Dehumidifying System
- mould temperature control system
- mould temperature controller
- mould temperature controllers
- New electric injection molding machine
- nitrogen dryer manufacturer
- nitrogen dryer system manufacturer
- Oil type mold temperature controller
- Oil type mold temperature controllers
- open day
- Outbound links: No outbound links appear in this page. Add some! Images: No images appear on this page. Add some! Internal links: No internal links appear in this page
- PET Preform injection molding
- phone case maker machine
- phone case making machine
- plastic bottle making machine
- plastic bottle manufacturing
- plastic bucket making machine
- plastic bucket manufacturing
- Plastic chair making machine
- plastic forming equipment
- plastic hopper dryer
- plastic injection machine
- plastic injection machines
- plastic injection molding
- Plastic injection molding equipment
- Plastic injection molding machine
- Plastic Injection Molding Machines
- plastic injection moulding machine
- plastic injection robot
- Plastic Molding machine
- Plastic Molding Machines
- plastic molding press
- plastic moulding machine
- plastic phone case making machine
- plastic-molding machine
- powerful granulator
- Powerful Type Sound-Proof Granulator
- precision injection molding
- precision injection molding machines
- production of plastic seats
- pure water mould temperature controller
- Robot injection molding
- robot injection molding machine
- robot manufacturing companies
- Robotic arm for injection molding machine
- robotic injection molding machines
- robotics in injection molding
- SCARA robot
- SCARA robots
- Service-oriented manufacturing
- Servo Cylinder Robot
- servo driven robot
- Servo Driven Robots
- servo injection robots
- servo motor-driven linear robots
- servo-driven 3-axis robot
- Servo-Driven Robot
- Setup of injection machine
- Silicone Injection Molding Machine
- six-axis industrial robot
- Stainless Hopper Dryer
- Stainless Hopper Dryers
- star club
- swing arm robot
- take-out robots
- the choice between servo-driven robots and hydraulic robots will have a certain impact on efficiency
- the most popular injection molding machine
- the type of injection molding robot
- toggle clamp injection molding machine
- Toggle Hydraulic Injection Molding Machines
- toggle injection molding machine
- Top 10 brands of injection robots
- Topstar
- Topstar Engineering
- Topstar Industrial Robots
- Topstar injection molding intelligent
- Topstar Scara Robots
- Useful Injection molding machine
- Vertical machining centers
- volumetric type blender
- water chiller
- water chillers
- water distributor
- water type mold temperature controller
- Water Type MoldTemperature Controller
- Water-Type Mould Temperature Controllers
- We often face choices when performing injection molding. We will choose the type of injection molding machine
- wholesale of injection molding machines
- x carve CNC