Highly automated injection molding material dehumidifying equipment
2024/04/27 By Topstar
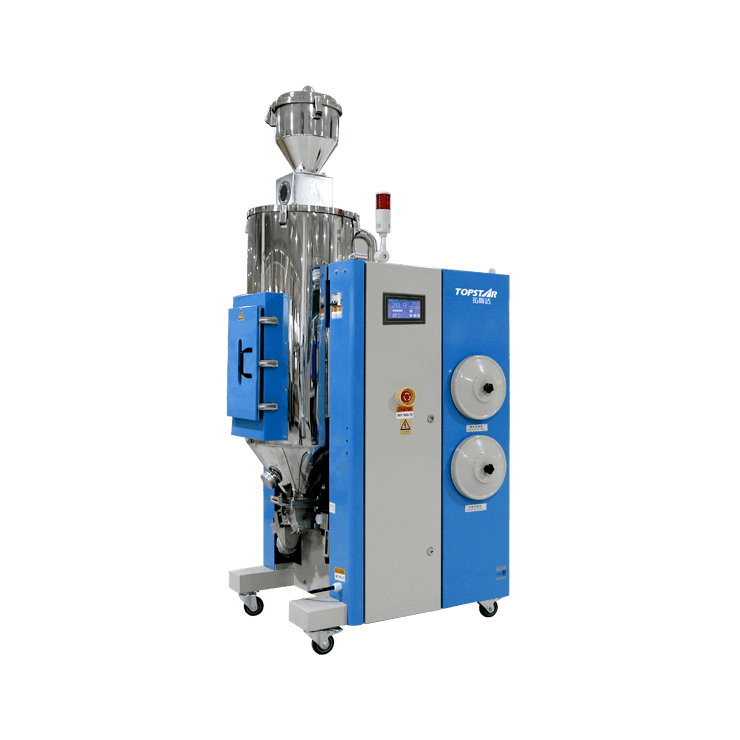
In injection molding, controlling raw material moisture is the key to directly determining the process and high-quality product results. Then, when dehumidifying injection molding materials, highly automated equipment is needed, which can be seamlessly integrated with the injection molding machine, is easy to operate, and has stable performance. This article will reveal the injection molding material dehumidifying equipment used in modern injection molding.
The necessity of dehumidification of injection molding materials
Dehumidifying the material during the injection molding process is a necessary step. The moisture in the material will affect the quality of the final product. Suppose hygroscopic materials are not dehumidified during the high-temperature processing of injection molding. In that case, the moisture acts as a catalyst to decompose the polymer chains, decreasing molecular weight. Adversely affects the mechanical properties of the polymer, resulting in a weaker, more brittle, and less durable product.
In addition, the moisture in the plastic particles can also cause some processing problems during the molding process. When moisture-filled plastic is heated in a syringe barrel, the water becomes steam and creates pressure within the material. This vapor can cause the material to foam, resulting in spatter on the surface of the molded part and voids or bubbles within the part, affecting aesthetics and structure. Insufficient dehumidification, especially for optical products, will affect the transparency and quality of the product.
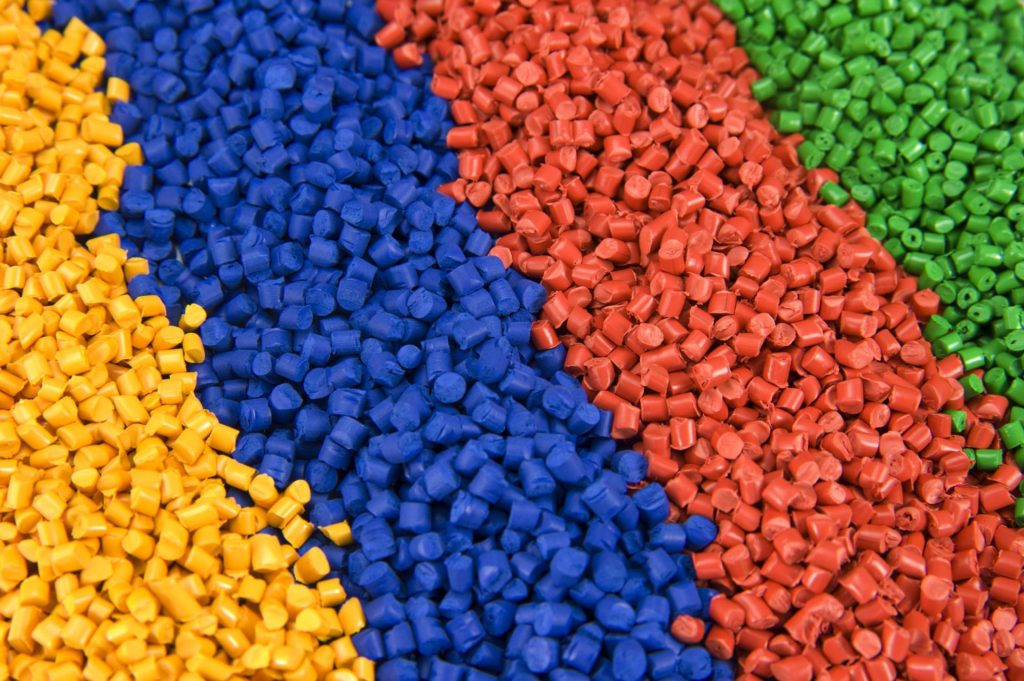
Characteristics of highly automated injection molding material dehumidifying systems
Topstar’s highly automated injection molding material dehumidification system usually integrates the three functions of dehumidification, drying, and feeding into one machine. This design takes up no space, is small, and has the entire machine controlled by a microcomputer. Their double-layer insulated drying barrel adopts a down-blowing air duct design, which can prevent heat loss and improve the drying effect. At the same time, it also has the characteristics of intelligent fault alarm and reservation start time. In particular, the dehumidification system adopts a double cooler structure to ensure lower return air temperature and dew point.
Adopt a double cooler structure
In the injection molding material dehumidifying equipment that integrates the three functions of dehumidification, drying, and feeding, the double cooler structure can reduce return air temperature and dew point, which is very important in dehumidification.
The dual cooler system divides the dehumidification process into two different cooling stages. The main cooler first cools the moist air extracted from the hopper, condensing most of the moisture in the air. The partially dried air then passes through a secondary cooler, reducing the air temperature below the initial dew point reached after the first cooling stage. This two-stage cooling process effectively reduces air temperature and dew point.
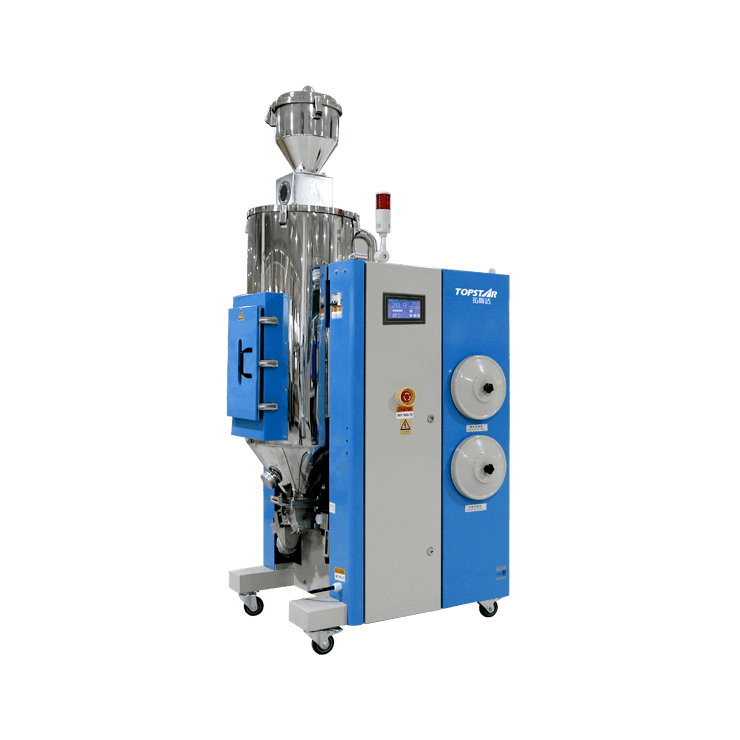
Stainless steel mirror polished
For some optical-grade products, there are special optical-grade models. All their raw material contact surfaces are stainless steel mirror polished and equipped with a closed loop feeding system to prevent the dried raw materials from regaining moisture due to contact with outside air.
The mirror-polished finish of this stainless steel is important to prevent contamination from plastic particles during the dehumidification process. It also ensures that no additional particulate or ionic contaminants enter the material, and the mirror-polished surface greatly reduces surface roughness, minimizing the areas where moisture and particulate matter can adhere. This smoothness also helps keep the system clean and reduces the build-up of residue, making mirror-polished stainless steel easier to clean than other materials with rough surfaces.
Integrate with existing injection molding operations
This dehumidification equipment for injection molding materials integrates the functions of dehumidification, drying, and feeding and can also be seamlessly integrated with the injection molding machine. This integration is achieved through a centralized control system synchronizing the dehumidification process with the molding operation. The central control system can communicate with dehumidification equipment and injection molding machines through a unified communication language to coordinate the time and quantity of processing materials. This ensures that we optimize material properties before they enter the mold. A PID temperature control system is also used to control the regeneration temperature accurately.
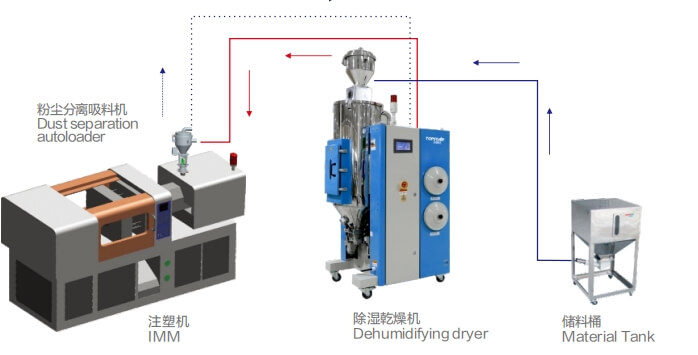
Keep injection molding materials dry
The highly automated injection molding material dehumidification equipment can obtain low dew point dry air with good stability by integrating dehumidification, drying, and feeding functions. The double cooler structure they adopt can ensure lower return air temperature and dew point. Integrating with injection molding equipment allows you to synchronize dehumidification and molding operations, making operations more convenient.
TRENDING POSTS
- What factors can cause delays in the injection molding process of plastic molding machine? 2024/04/27
- Exhibition Review| Topstar participates in InterPlas Thailand 2024 2024/04/27
- Star Case | Topstar helps Santong upgrade its intelligent plant 2024/04/27
- Topstar Special | National Science and Technology Workers Day 2024/04/27
HOT TOPIC
- 3 in 1 Compact Dehumidifying Dryer
- 5-axis CNC machine
- accuracy
- Air Chillers
- all electric injection molding machine
- All-electric injection molding machines
- and overall production quality. Therefore
- AP-RubberPlas
- automated injection molding machine
- Automation changed engineering
- automation of injection molding robots
- auxiliary machine
- Bench Injection Molding Machine
- Cabinet dryer manufacturers
- Cabinet dryers
- chiller
- CNC Drilling Machine
- CNC Drilling Machines
- cnc engraving machine manufacturer
- cnc laser cutting machine manufacturer
- CNC machine
- CNC Machine Center
- CNC Machine for Sale
- CNC Machine Manufacturing
- CNC Machine Tool
- CNC machine tool product
- CNC Machining Center
- CNC wood carving machine
- Cooling system
- Cross-Walking Single Axis Servo Cylinder Robot
- Cross-Walking Single-Axis Servo Cylinder Robot
- Cross-Walking Three-Axis/Five-Axis Servo Driven Robot
- cross-walking three-axis/five-axis servo-driven robot
- Dehumidifier Dryer
- Dehumidifying Dryer
- delta parallel robot
- Desktop Injection Molding Machine
- Desktop injection molding machines
- Desktop Molding Machine
- desktop plastic injection machine
- Desktop Plastic Injection Molding Machine
- direct clamp injection molding machine
- Direct clamp injection molding machines
- Dosing & mixing system
- Drilling Centers
- Drying and dehumidification system
- drying and dehumidifying equipment
- Drying and Dehumidifying System
- drying system
- effective and efficient. Cabinet dryers are also used in other industries where large quantities of material need to be dried
- efficient injection molding machine
- elbow hydraulic injection molding machines
- electric injection molding machine
- electric injection molding machines
- etc. Among injection molding robots
- exhibition
- features of CNC machine
- Feeding And Conveying System
- Five Axis Machine Center
- Fully automatic injection molding machine
- Gathering Topstar
- giant injection molding machine
- GMU-600 5-Axis Machining Center
- Granulating & Recycling System
- Heavy duty injection molding machine
- Honeycomb rotor dehumidifier
- horizontal injection molding machine
- Horizontal Injection Molding Machines
- Horizontal Injection Moulding Machine
- Horizontal Mixer manufacturer
- How The CNC Machine Works
- hybrid injection molding machine
- hydraulic injection molding machine
- Hydraulic Injection Molding Machines
- in this article
- Industrial robot
- Industrial Robot Chinese brand
- industrial robot parts
- industrial robot supplier
- Industrial robots
- Industry Chain
- Injection Manipulator
- injection mold machines
- Injection molding
- Injection molding automation
- Injection Molding Automation Solution
- injection molding dryer
- Injection molding equipment
- injection molding hopper dryer
- Injection molding machine
- injection molding machine brand
- Injection Molding Machine Factory
- Injection Molding Machine Manufacture
- Injection molding machine manufacturer
- injection molding machine manufacturers
- Injection molding machine procurement
- injection molding machine robotic arm
- injection molding machine with a robot
- Injection molding machines
- injection molding material dehumidifying
- injection molding plant
- Injection Molding Robot
- injection molding robot arm
- Injection molding robot automation
- Injection molding robotic arm
- injection molding robots
- Injection Moulding Robots
- Injection Robot
- Injection robot arm
- Injection robot manufacturer
- Injection robot wholesale
- injection robots
- intelligent injection molding machines
- Introducing Injection Robot
- It is the best choice for drying large quantities of material at once. Cabinetmakers use these machines because they are fast
- large injection molding machine
- Learn what industrial automation and robotics is
- low speed sound-proof granulator
- machine plastic molding
- make sure to add some! Improvements (2) Keyphrase in introduction: Your keyphrase or its synonyms appear in the first paragraph of the copy
- manipulator machine
- manufacturing
- micro injection molding machine
- middle speed granulator
- Mini CNC machine manufacturers.
- Mold Temperature Control System
- mold temperature controller
- molding material Dehumidifying System
- mould temperature controller
- mould temperature controllers
- New electric injection molding machine
- nitrogen dryer manufacturer
- nitrogen dryer system manufacturer
- Oil type mold temperature controller
- open day
- Outbound links: No outbound links appear in this page. Add some! Images: No images appear on this page. Add some! Internal links: No internal links appear in this page
- PET Preform injection molding
- phone case maker machine
- phone case making machine
- plastic bottle making machine
- plastic bottle manufacturing
- plastic bucket making machine
- plastic bucket manufacturing
- Plastic chair making machine
- plastic forming equipment
- plastic hopper dryer
- plastic injection machine
- plastic injection machines
- plastic injection molding
- Plastic injection molding equipment
- Plastic injection molding machine
- Plastic Injection Molding Machines
- plastic injection robot
- Plastic Molding machine
- Plastic Molding Machines
- plastic molding press
- plastic phone case making machine
- plastic-molding machine
- powerful granulator
- Powerful Type Sound-Proof Granulator
- production of plastic seats
- Robot injection molding
- robot injection molding machine
- robot manufacturing companies
- Robotic arm for injection molding machine
- robotic injection molding machines
- robotics in injection molding
- SCARA robot
- SCARA robots
- Service-oriented manufacturing
- Servo Cylinder Robot
- servo driven robot
- Servo Driven Robots
- servo injection robots
- Servo-Driven Robot
- Setup of injection machine
- Silicone Injection Molding Machine
- six-axis industrial robot
- Stainless Hopper Dryer
- Stainless Hopper Dryers
- star club
- swing arm robot
- the choice between servo-driven robots and hydraulic robots will have a certain impact on efficiency
- the most popular injection molding machine
- the type of injection molding robot
- toggle clamp injection molding machine
- Toggle Hydraulic Injection Molding Machines
- toggle injection molding machine
- Top 10 brands of injection robots
- Topstar
- Topstar Engineering
- Topstar Industrial Robots
- Topstar injection molding intelligent
- Topstar Scara Robots
- Useful Injection molding machine
- Vertical machining centers
- volumetric type blender
- water chiller
- water chillers
- water distributor
- Water Type MoldTemperature Controller
- We often face choices when performing injection molding. We will choose the type of injection molding machine
- wholesale of injection molding machines
- x carve CNC