Plastic injection molding machine with stable performance
2024/04/26 By Topstar
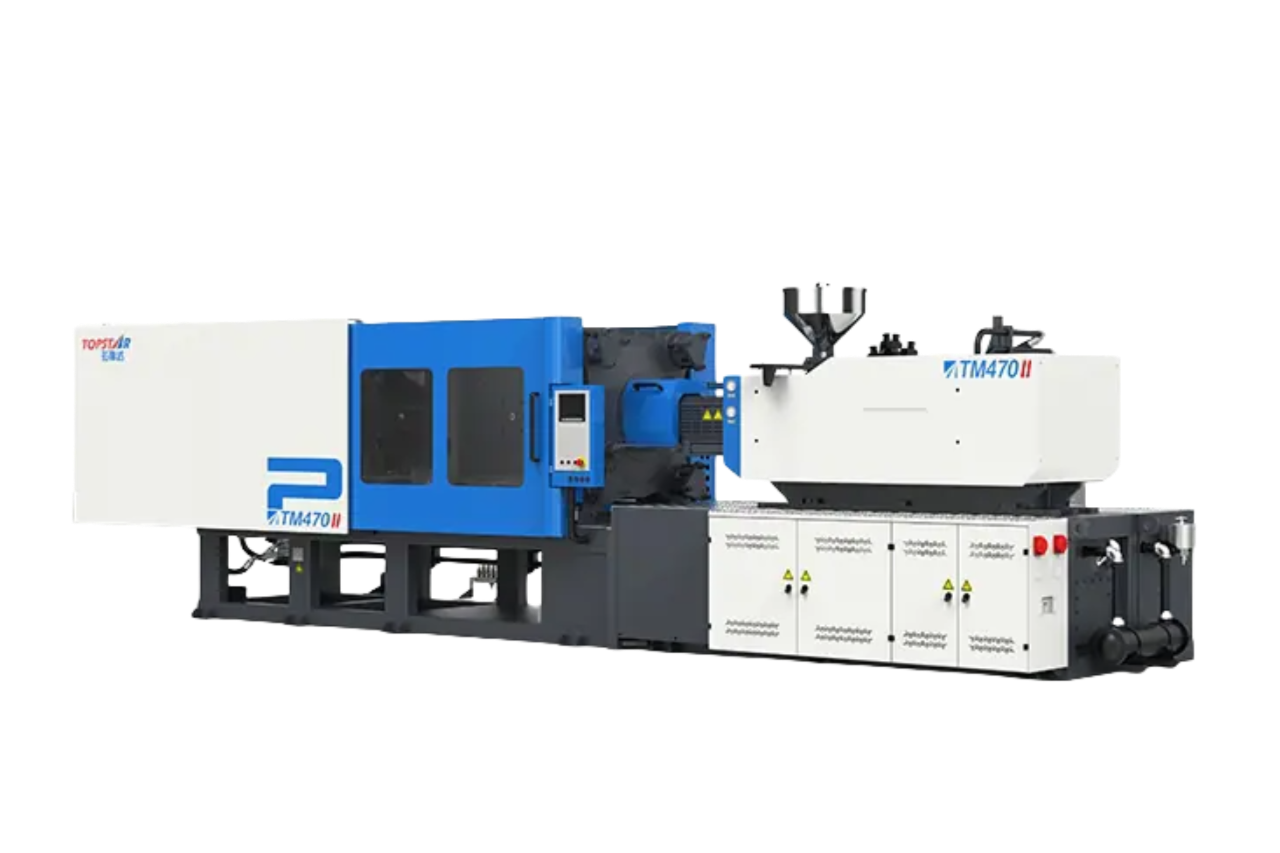
In the rapidly developing plastics manufacturing industry, plastic injection molding machines are key equipment for producing complex, high-quality plastic parts. Therefore, their stability is very important. However, problems that affect efficiency and instability often occur in traditional plastic injection molding machines. Then, this article will share with you the conditions for a stable plastic injection molding machine and the limitations of tradition.
Instability problems of traditional plastic injection molding machine
The instability of the injection molding machine is mainly caused by fluctuations in temperature, pressure, and other process parameters. Temperature control is critical during the injection molding process, affecting the polymer’s flow and the final product’s quality. If the heating element is old or faulty and the heat regulation system is insufficient, the problem of inaccurate temperature control can arise. Leakage or wear of seals and pumps causes hydraulic instability in injection molding, which can lead to problems such as short shots or flooding. In addition, inconsistent screw movement may also lead to pressure instability. Over time, components such as toggle joints, tie rods, and mold clamps in traditional injection molding machines may wear out, leading to instability during molding, such as misalignment and uneven clamping force.
Technical progress of plastic injection molding machine
Driven by Industry 4.0, the overall plastic injection molding machine has been improved. The hydraulic plastic injection molding machine adopts a five-point hinge structure, which makes the performance more stable and reliable, and the overall cost performance is higher. In addition, we integrate the belt-driven servo motor into the electric injection molding machine. Using the motor to control movement with high precision reduces energy consumption by up to 70%, which can shorten cycle times and improve product quality. In addition, they can also realize signal interconnection with surrounding injection molding auxiliary equipment through bus communication. It makes your operation more concise and efficient, and the cooperation between equipment is more stable.
The use of a super template design is more stable
One way to enhance the stability of plastic injection molding machines is to integrate “super template” designs into their mechanisms. Super platen design refers to a highly strong and rigid platen design that minimizes deflection during injection and clamping cycles. The materials used in super formwork designs, typically high-grade alloy steels with high tensile strength and durability, ensure the platen can withstand the pressures and stresses of injection molding without compromising its structural integrity. In addition, it can evenly distribute the clamping force on the mold surface and also has the function of automatically and accurately adjusting the mold with one click.
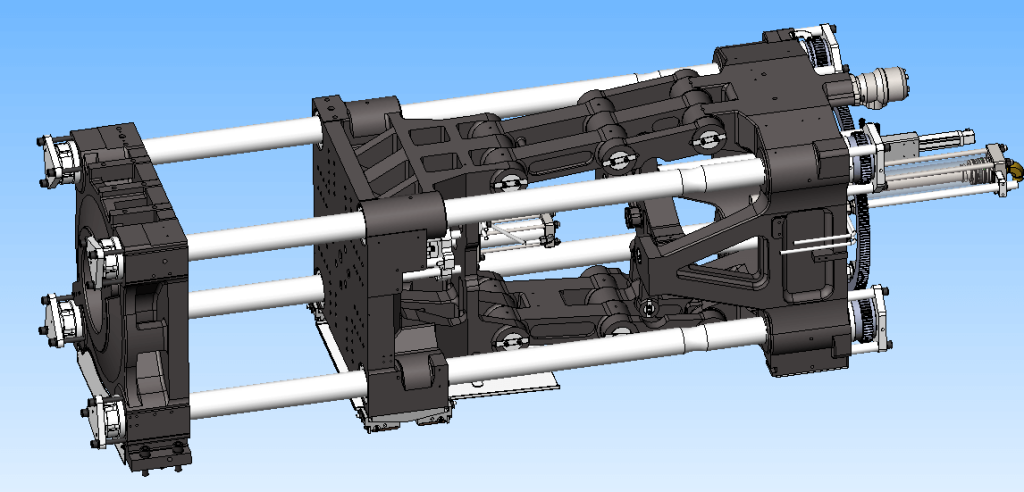
Intelligent electric mold opening and closing
An intelligent electric mold opening and closing system is integrated into the electric plastic injection molding machine. The core servo-electric drive can accurately control the mold opening and closing mechanism. Ensures stable clamping force throughout the injection cycle, helping reduce problems such as flash, uneven part walls, or warpage.
Electric injection molding machines offer excellent repeatability thanks to their precise control systems. The servo-electric drive has precise positioning accuracy, which can be controlled within 0.01 mm, ensuring the mold opens and closes to the same position every cycle. The intelligent electric mold opening and closing system sensor can detect any abnormal resistance during the mold closing stage, such as incorrect gripping position. Once detected, the system can stop the mold closing process, preventing damage to the mold or machine.
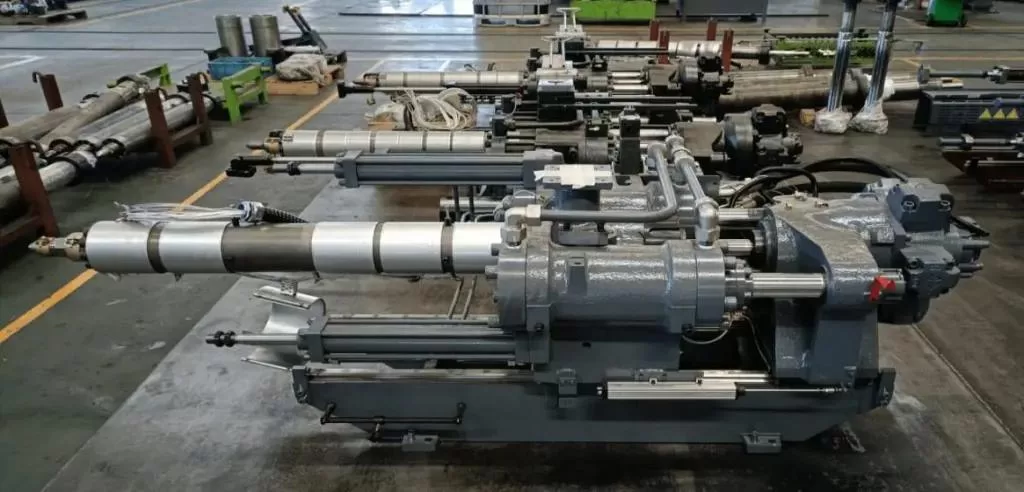
Adopt an integrated high-rigidity shooting base structure
Another key feature of the stability of modern plastic injection molding machines is the integration of a highly rigid injection base structure. This rigidity directly affects the accuracy of the injection process and the quality of the molded part, and also ensures that the base can withstand the stress of repeated injection cycles without deforming.
This integrated structure distributes pressure evenly throughout the structure, eliminating single weak joints or bending points. In addition, the highly rigid injection base prevents vibration and torsional movement during the injection process. If these movements are present in injection molding, they can also lead to inconsistent injection weights, pressure, and problems with part size and surface finish.
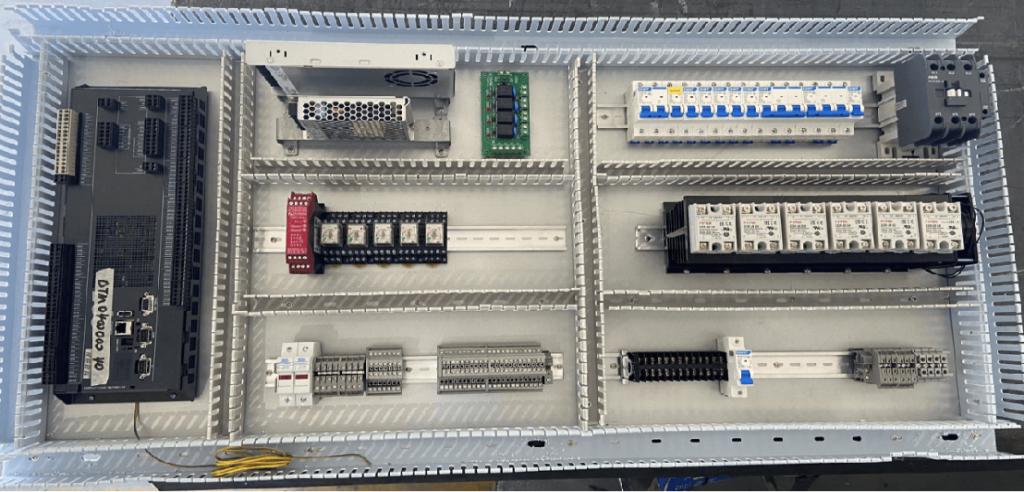
Importance of stability
Plastic injection molding machines can maintain stable output, and infrequent failures can greatly improve the efficiency of the entire production line and ensure that the final plastic products are consistently of high quality. This stability is necessary for manufacturers.
TRENDING POSTS
- What factors can cause delays in the injection molding process of plastic molding machine? 2024/04/26
- Exhibition Review| Topstar participates in InterPlas Thailand 2024 2024/04/26
- Star Case | Topstar helps Santong upgrade its intelligent plant 2024/04/26
- Topstar Special | National Science and Technology Workers Day 2024/04/26
HOT TOPIC
- 3 in 1 Compact Dehumidifying Dryer
- 5-axis CNC machine
- accuracy
- Air Chillers
- all electric injection molding machine
- All-electric injection molding machines
- and overall production quality. Therefore
- AP-RubberPlas
- automated injection molding machine
- Automation changed engineering
- automation of injection molding robots
- auxiliary machine
- Bench Injection Molding Machine
- Cabinet dryer manufacturers
- Cabinet dryers
- chiller
- CNC Drilling Machine
- CNC Drilling Machines
- cnc engraving machine manufacturer
- cnc laser cutting machine manufacturer
- CNC machine
- CNC Machine Center
- CNC Machine for Sale
- CNC Machine Manufacturing
- CNC Machine Tool
- CNC machine tool product
- CNC Machining Center
- CNC wood carving machine
- Cooling system
- Cross-Walking Single Axis Servo Cylinder Robot
- Cross-Walking Single-Axis Servo Cylinder Robot
- Cross-Walking Three-Axis/Five-Axis Servo Driven Robot
- cross-walking three-axis/five-axis servo-driven robot
- Dehumidifier Dryer
- Dehumidifying Dryer
- delta parallel robot
- Desktop Injection Molding Machine
- Desktop injection molding machines
- Desktop Molding Machine
- desktop plastic injection machine
- Desktop Plastic Injection Molding Machine
- direct clamp injection molding machine
- Direct clamp injection molding machines
- Dosing & mixing system
- Drilling Centers
- Drying and dehumidification system
- drying and dehumidifying equipment
- Drying and Dehumidifying System
- drying system
- effective and efficient. Cabinet dryers are also used in other industries where large quantities of material need to be dried
- efficient injection molding machine
- elbow hydraulic injection molding machines
- electric injection molding machine
- electric injection molding machines
- etc. Among injection molding robots
- exhibition
- features of CNC machine
- Feeding And Conveying System
- Five Axis Machine Center
- Fully automatic injection molding machine
- Gathering Topstar
- giant injection molding machine
- GMU-600 5-Axis Machining Center
- Granulating & Recycling System
- Heavy duty injection molding machine
- Honeycomb rotor dehumidifier
- horizontal injection molding machine
- Horizontal Injection Molding Machines
- Horizontal Injection Moulding Machine
- Horizontal Mixer manufacturer
- How The CNC Machine Works
- hybrid injection molding machine
- hydraulic injection molding machine
- Hydraulic Injection Molding Machines
- in this article
- Industrial robot
- Industrial Robot Chinese brand
- industrial robot parts
- industrial robot supplier
- Industrial robots
- Industry Chain
- Injection Manipulator
- injection mold machines
- Injection molding
- Injection molding automation
- Injection Molding Automation Solution
- injection molding dryer
- Injection molding equipment
- injection molding hopper dryer
- Injection molding machine
- injection molding machine brand
- Injection Molding Machine Factory
- Injection Molding Machine Manufacture
- Injection molding machine manufacturer
- injection molding machine manufacturers
- Injection molding machine procurement
- injection molding machine robotic arm
- injection molding machine with a robot
- Injection molding machines
- injection molding material dehumidifying
- injection molding plant
- Injection Molding Robot
- injection molding robot arm
- Injection molding robot automation
- Injection molding robotic arm
- injection molding robots
- Injection Moulding Robots
- Injection Robot
- Injection robot arm
- Injection robot manufacturer
- Injection robot wholesale
- injection robots
- intelligent injection molding machines
- Introducing Injection Robot
- It is the best choice for drying large quantities of material at once. Cabinetmakers use these machines because they are fast
- large injection molding machine
- Learn what industrial automation and robotics is
- low speed sound-proof granulator
- machine plastic molding
- make sure to add some! Improvements (2) Keyphrase in introduction: Your keyphrase or its synonyms appear in the first paragraph of the copy
- manipulator machine
- manufacturing
- micro injection molding machine
- middle speed granulator
- Mini CNC machine manufacturers.
- Mold Temperature Control System
- mold temperature controller
- molding material Dehumidifying System
- mould temperature controller
- mould temperature controllers
- New electric injection molding machine
- nitrogen dryer manufacturer
- nitrogen dryer system manufacturer
- Oil type mold temperature controller
- open day
- Outbound links: No outbound links appear in this page. Add some! Images: No images appear on this page. Add some! Internal links: No internal links appear in this page
- PET Preform injection molding
- phone case maker machine
- phone case making machine
- plastic bottle making machine
- plastic bottle manufacturing
- plastic bucket making machine
- plastic bucket manufacturing
- Plastic chair making machine
- plastic forming equipment
- plastic hopper dryer
- plastic injection machine
- plastic injection machines
- plastic injection molding
- Plastic injection molding equipment
- Plastic injection molding machine
- Plastic Injection Molding Machines
- plastic injection robot
- Plastic Molding machine
- Plastic Molding Machines
- plastic molding press
- plastic phone case making machine
- plastic-molding machine
- powerful granulator
- Powerful Type Sound-Proof Granulator
- production of plastic seats
- Robot injection molding
- robot injection molding machine
- robot manufacturing companies
- Robotic arm for injection molding machine
- robotic injection molding machines
- robotics in injection molding
- SCARA robot
- SCARA robots
- Service-oriented manufacturing
- Servo Cylinder Robot
- servo driven robot
- Servo Driven Robots
- servo injection robots
- Servo-Driven Robot
- Setup of injection machine
- Silicone Injection Molding Machine
- six-axis industrial robot
- Stainless Hopper Dryer
- Stainless Hopper Dryers
- star club
- swing arm robot
- the choice between servo-driven robots and hydraulic robots will have a certain impact on efficiency
- the most popular injection molding machine
- the type of injection molding robot
- toggle clamp injection molding machine
- Toggle Hydraulic Injection Molding Machines
- toggle injection molding machine
- Top 10 brands of injection robots
- Topstar
- Topstar Engineering
- Topstar Industrial Robots
- Topstar injection molding intelligent
- Topstar Scara Robots
- Useful Injection molding machine
- Vertical machining centers
- volumetric type blender
- water chiller
- water chillers
- water distributor
- Water Type MoldTemperature Controller
- We often face choices when performing injection molding. We will choose the type of injection molding machine
- wholesale of injection molding machines
- x carve CNC