Injection molding hopper dryer that integrates three functions
2024/04/03 By Topstar
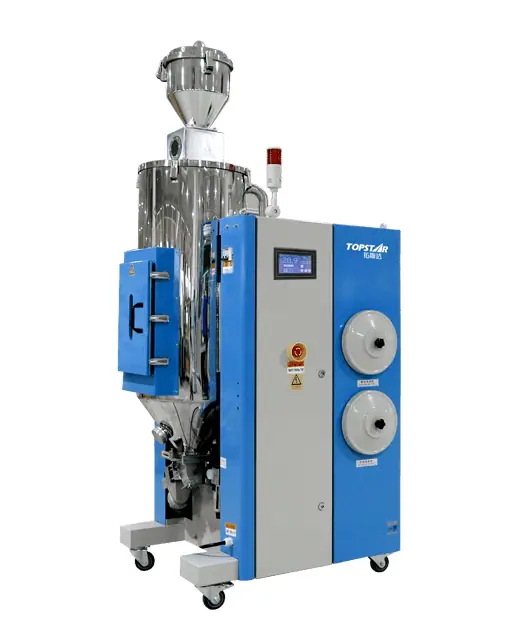
One of the tasks that will be performed in any workshop that manufactures plastic products is the drying, conveying, and dehumidification of raw materials. These three tasks usually require three different pieces of equipment to complete, which wastes money, takes up space, is inefficient, etc. Topstar’s auxiliary equipment series can integrate these three functions into one injection molding hopper dryer. In this guide, we’ll introduce the concept of a three-function plastic hopper dryer and how it can improve your performance.
Drying function of Injection molding hopper dryer
The main function of the three-in-one injection molding machine hopper dryer is to dry plastic raw materials. We adopt a down-blowing air duct design in the drying hopper to prevent heat loss, improve drying efficiency, and control the resin particles in the hopper. Heat promotes the evaporation of water in its raw materials. The powerful airflow system evenly circulates hot air to the entire hopper chamber, drying the resin particles evenly and preventing local overheating or moisture retention. Each model has a honeycomb runner to obtain low dew point dry air with good stability. It can also precisely control the temperature through the PID temperature control system to ensure the stability of the dew point.
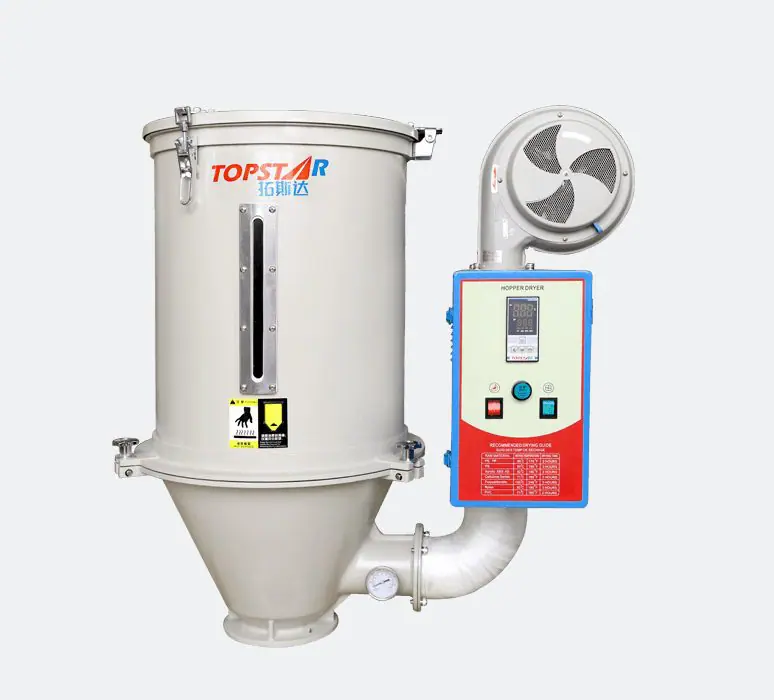
Conveying function of injection plastic hopper dryer
As for the conveying function of the three-in-one injection molding hopper dryer, we combine it with a stainless steel two-stage or three-stage feeder, and the feeding system is equipped with a cut-off valve so that there is no residual raw material in the material pipe during the feeding process. They use compressed air to transport dry granules from the hopper dryer to the hopper of the injection molding machine through a network of sealed pipes. This approach offers several advantages, including reduced risk of contamination and increased flexibility in delivering pellets to multiple molding machines in a centralized production setup. This function can also adjust the conveying time through the controller.
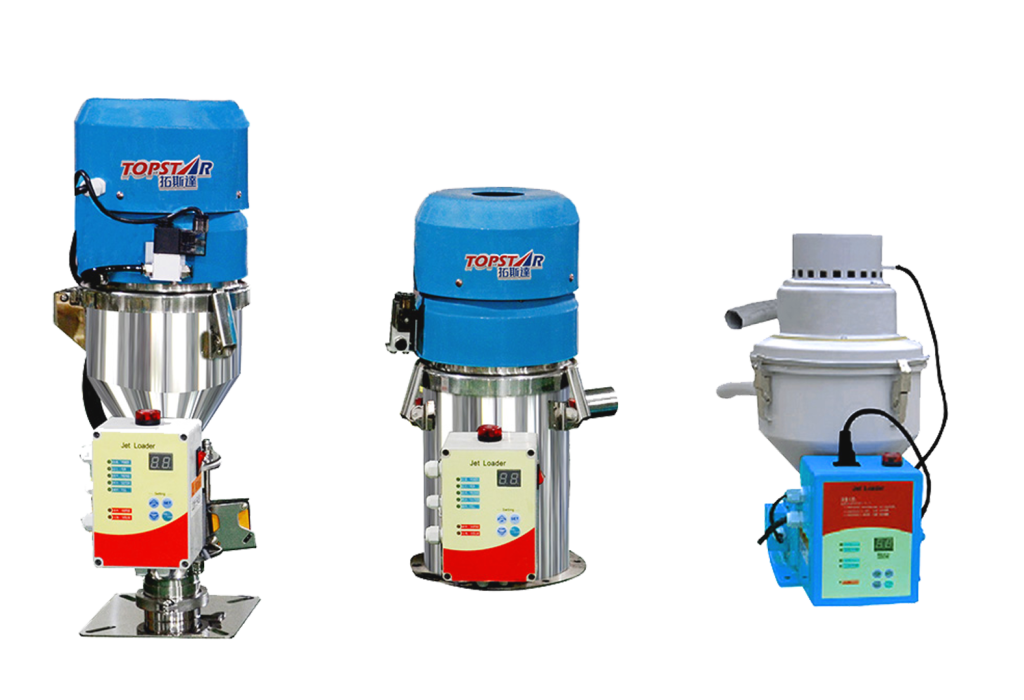
Dehumidification function of Injection molding hopper dryer
The last one is their dehumidification function, the core component of which is the ceramic honeycomb rotary dehumidifier. They can evenly grow moisture-absorbing silica gel and molecular sieves on the ceramic fiber, making it extremely hygroscopic. Therefore, using this wheel, the dehumidifier can reach a low dew point of -40°C and greatly improve efficiency. They pass moist air through a desiccant material or refrigeration coil, where the moisture condenses and is subsequently removed, leaving behind dry air to aid in drying. To optimize the dehumidification process, we can also monitor and adjust the humidity level in the drying chamber via the controller.
Enhance overall drying performance!
Integrating drying, conveying, and dehumidification functions into a single device simplifies your production process and reduces the need for separate drying, dehumidification, and conveying equipment. At the same time, optimized material preparation also helps improve overall operational efficiency and cost-effectiveness, simplifies maintenance, and reduces energy consumption. In addition, it can also design an optical-grade three-in-one dehumidification dryer for optical-grade products. We stainless steel mirror polish all raw material contact surfaces of the optical-grade model and equip them with a closed-loop feeding system to prevent the dried raw materials from contacting the outside air and becoming damp again.
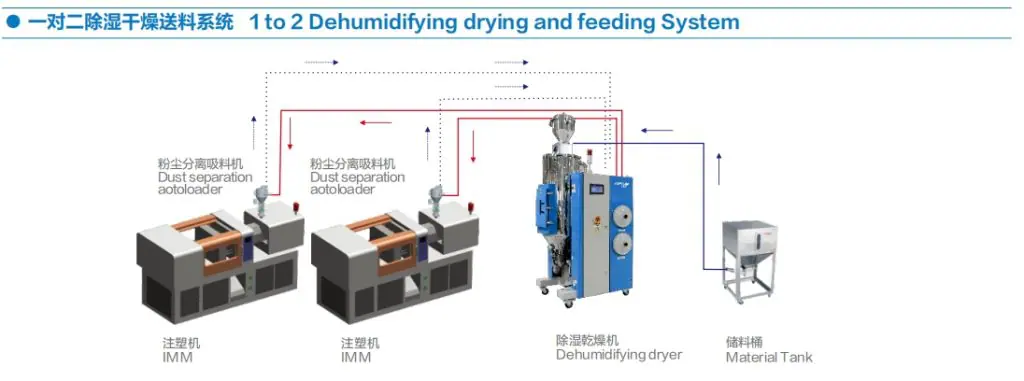
Suitable applications
The three-in-one injection molding hopper dryer is suitable for drying and conveying raw materials in the injection molding industry, extrusion industry, medical industry, food industry, optical industry, electronics industry, automobile industry, etc. They are suitable for drying a wide range of resins including ABS, PET, PVC, and nylon, making them a versatile solution equipment for manufacturers with different production needs. Whether it is producing small precision parts or large structural parts, the injection plastic hopper dryer can ensure the quality and performance of the final product and is a high-quality and efficient drying and conveying system.
Ultimately
Integrating drying, conveying and dehumidification functions into an injection molding hopper dryer provides manufacturers with a simplified and efficient resin conditioning solution. The three-in-one injection molding hopper dryer can improve product quality, reduce production costs, and achieve a drying and conveying system with stable performance and low energy consumption.
TRENDING POSTS
- What factors can cause delays in the injection molding process of plastic molding machine? 2024/04/03
- Exhibition Review| Topstar participates in InterPlas Thailand 2024 2024/04/03
- Star Case | Topstar helps Santong upgrade its intelligent plant 2024/04/03
- Topstar Special | National Science and Technology Workers Day 2024/04/03
HOT TOPIC
- 3 in 1 Compact Dehumidifying Dryer
- 5-axis CNC machine
- accuracy
- Air Chillers
- all electric injection molding machine
- All-electric injection molding machines
- and overall production quality. Therefore
- AP-RubberPlas
- automated injection molding machine
- Automation changed engineering
- automation of injection molding robots
- auxiliary machine
- Bench Injection Molding Machine
- Cabinet dryer manufacturers
- Cabinet dryers
- chiller
- CNC Drilling Machine
- CNC Drilling Machines
- cnc engraving machine manufacturer
- cnc laser cutting machine manufacturer
- CNC machine
- CNC Machine Center
- CNC Machine for Sale
- CNC Machine Manufacturing
- CNC Machine Tool
- CNC machine tool product
- CNC Machining Center
- CNC wood carving machine
- Cooling system
- Cross-Walking Single Axis Servo Cylinder Robot
- Cross-Walking Single-Axis Servo Cylinder Robot
- Cross-Walking Three-Axis/Five-Axis Servo Driven Robot
- cross-walking three-axis/five-axis servo-driven robot
- Dehumidifier Dryer
- Dehumidifying Dryer
- delta parallel robot
- Desktop Injection Molding Machine
- Desktop injection molding machines
- Desktop Molding Machine
- desktop plastic injection machine
- Desktop Plastic Injection Molding Machine
- direct clamp injection molding machine
- Direct clamp injection molding machines
- Dosing & mixing system
- Drilling Centers
- Drying and dehumidification system
- drying and dehumidifying equipment
- Drying and Dehumidifying System
- drying system
- effective and efficient. Cabinet dryers are also used in other industries where large quantities of material need to be dried
- efficient injection molding machine
- elbow hydraulic injection molding machines
- electric injection molding machine
- electric injection molding machines
- etc. Among injection molding robots
- exhibition
- features of CNC machine
- Feeding And Conveying System
- Five Axis Machine Center
- Fully automatic injection molding machine
- Gathering Topstar
- giant injection molding machine
- GMU-600 5-Axis Machining Center
- Granulating & Recycling System
- Heavy duty injection molding machine
- Honeycomb rotor dehumidifier
- horizontal injection molding machine
- Horizontal Injection Molding Machines
- Horizontal Injection Moulding Machine
- Horizontal Mixer manufacturer
- How The CNC Machine Works
- hybrid injection molding machine
- hydraulic injection molding machine
- Hydraulic Injection Molding Machines
- in this article
- Industrial robot
- Industrial Robot Chinese brand
- industrial robot parts
- industrial robot supplier
- Industrial robots
- Industry Chain
- Injection Manipulator
- injection mold machines
- Injection molding
- Injection molding automation
- Injection Molding Automation Solution
- injection molding dryer
- Injection molding equipment
- injection molding hopper dryer
- Injection molding machine
- injection molding machine brand
- Injection Molding Machine Factory
- Injection Molding Machine Manufacture
- Injection molding machine manufacturer
- injection molding machine manufacturers
- Injection molding machine procurement
- injection molding machine robotic arm
- injection molding machine with a robot
- Injection molding machines
- injection molding material dehumidifying
- injection molding plant
- Injection Molding Robot
- injection molding robot arm
- Injection molding robot automation
- Injection molding robotic arm
- injection molding robots
- Injection Moulding Robots
- Injection Robot
- Injection robot arm
- Injection robot manufacturer
- Injection robot wholesale
- injection robots
- intelligent injection molding machines
- Introducing Injection Robot
- It is the best choice for drying large quantities of material at once. Cabinetmakers use these machines because they are fast
- large injection molding machine
- Learn what industrial automation and robotics is
- low speed sound-proof granulator
- machine plastic molding
- make sure to add some! Improvements (2) Keyphrase in introduction: Your keyphrase or its synonyms appear in the first paragraph of the copy
- manipulator machine
- manufacturing
- micro injection molding machine
- middle speed granulator
- Mini CNC machine manufacturers.
- Mold Temperature Control System
- mold temperature controller
- molding material Dehumidifying System
- mould temperature controller
- mould temperature controllers
- New electric injection molding machine
- nitrogen dryer manufacturer
- nitrogen dryer system manufacturer
- Oil type mold temperature controller
- open day
- Outbound links: No outbound links appear in this page. Add some! Images: No images appear on this page. Add some! Internal links: No internal links appear in this page
- PET Preform injection molding
- phone case maker machine
- phone case making machine
- plastic bottle making machine
- plastic bottle manufacturing
- plastic bucket making machine
- plastic bucket manufacturing
- Plastic chair making machine
- plastic forming equipment
- plastic hopper dryer
- plastic injection machine
- plastic injection machines
- plastic injection molding
- Plastic injection molding equipment
- Plastic injection molding machine
- Plastic Injection Molding Machines
- plastic injection robot
- Plastic Molding machine
- Plastic Molding Machines
- plastic molding press
- plastic phone case making machine
- plastic-molding machine
- powerful granulator
- Powerful Type Sound-Proof Granulator
- production of plastic seats
- Robot injection molding
- robot injection molding machine
- robot manufacturing companies
- Robotic arm for injection molding machine
- robotic injection molding machines
- robotics in injection molding
- SCARA robot
- SCARA robots
- Service-oriented manufacturing
- Servo Cylinder Robot
- servo driven robot
- Servo Driven Robots
- servo injection robots
- Servo-Driven Robot
- Setup of injection machine
- Silicone Injection Molding Machine
- six-axis industrial robot
- Stainless Hopper Dryer
- Stainless Hopper Dryers
- star club
- swing arm robot
- the choice between servo-driven robots and hydraulic robots will have a certain impact on efficiency
- the most popular injection molding machine
- the type of injection molding robot
- toggle clamp injection molding machine
- Toggle Hydraulic Injection Molding Machines
- toggle injection molding machine
- Top 10 brands of injection robots
- Topstar
- Topstar Engineering
- Topstar Industrial Robots
- Topstar injection molding intelligent
- Topstar Scara Robots
- Useful Injection molding machine
- Vertical machining centers
- volumetric type blender
- water chiller
- water chillers
- water distributor
- Water Type MoldTemperature Controller
- We often face choices when performing injection molding. We will choose the type of injection molding machine
- wholesale of injection molding machines
- x carve CNC