How do you find the manipulator machine that’s right for you?
2024/04/05 By Topstar
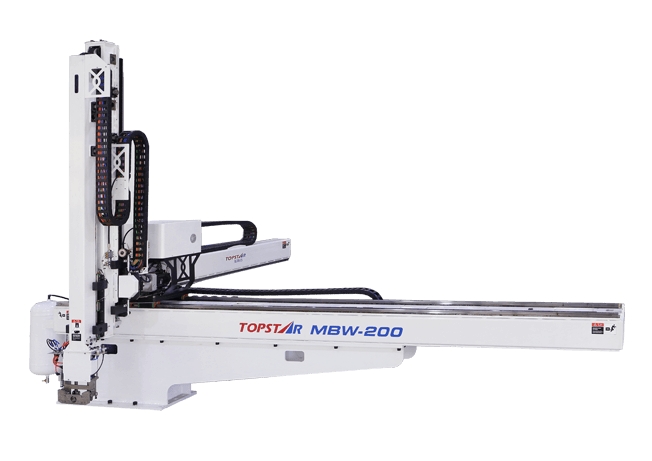
Every user who uses an injection molding machine will ask us how to find the right manipulator machine for you when purchasing an injection molding machine. The manipulator machine is installed above the injection molding machine and uses mechanical arms to grab and pick up plastic products in different directions. This guide will share the methods and considerations for finding the right manipulator machine.
Learn about manipulator machine specification options!
Payload capacity is one of the main specifications when choosing a manipulator machine. This refers to the maximum weight the robot can handle, including the weight of any end-of-arm tools or payload it carries. Usually, we need to choose based on the type of injection molding machine and the products being molded. The common load capacity is between 3kg and 20kg.
Another specification is the working range of the manipulator machine, which determines the maximum distance it can reach from its base while performing a task. They usually measure their reach from the center of their base to the ends of their arms. A robot with the right manipulator for you can perform tasks efficiently without repositioning. The last thing is their speed and accuracy. High-speed and high-precision robots are crucial for applications that require fast and precise movement and can greatly improve work efficiency.
Match manipulator machine feature specifications to your needs!
The next step is to match your needs with the functional specifications of the robot. For example, when you produce long-shaped heavy-duty products, such as car bumpers, door trims, and large home appliance casings, a robot with a 50kg load range is suitable. On the contrary, if you are producing small products such as automotive connectors and 3C electronics, then using a robot with a load range of 3kg is suitable. In addition, we can customize specialized end-of-arm tools to suit your needs, such as vision systems for guidance and inspection, and force/torque sensors to detect and react to environmental changes. By matching the capabilities of your manipulator machine to your needs, you can maximize the efficiency and productivity of your injection molding operation.
Ease of manipulator machine integration
Once you’ve selected the features that match your needs, look for robotic machines that can integrate with your existing injection molding machinery and automation systems. Considering their compatibility and programming with industry-standard communication protocols, general manipulator robots can support MODBUS RTU communication protocol and come standard with the RS485 communication interface. Whether you’re in manufacturing, logistics, healthcare, or any other industry, manipulator robots need to integrate seamlessly into your workflow and work with operators and other automated systems to optimize efficiency and productivity.
Assess reliability to ensure long-term performance!
Manipulator robots are a very important investment. Their reliability can greatly increase productivity and significantly reduce downtime. Therefore, we must look for companies that produce high-quality, reliable products and provide excellent customer support. A reputable manufacturer will likely provide a reliable robot that meets your expectations. High-quality materials and components are essential to ensure long-term durability and reliability. Robotic machines using high-quality materials and components, all sourced from reputable suppliers.
Commissioning and performance testing
After you have selected the right manipulator robot, you need to install and configure the robot according to the manufacturer’s specifications. Make sure all components are properly connected, calibrated, and programmed. And perform a thorough system check and diagnosis before testing. First, perform basic functional testing.
Test each motion axis, end effector functionality, sensor inputs, and communication interfaces. Once the basic functions are established, performance testing will be performed to test their speed, accuracy, repeatability, and cycle time under various operating conditions and load scenarios. Then, there are safety tests to test their emergency stop functions and collision detection systems when encountering dangerous collisions. Finally, interoperability and compatibility should be verified when integrating them with other devices.
Ultimately
Once you fully understand your needs and conduct extensive research on the robot’s technical specifications, integrated features, and reliability, you can make a decision to select a machine that provides the perfect balance of functionality, performance, and value for your specific injection molding operation.
TRENDING POSTS
- What factors can cause delays in the injection molding process of plastic molding machine? 2024/04/05
- Exhibition Review| Topstar participates in InterPlas Thailand 2024 2024/04/05
- Star Case | Topstar helps Santong upgrade its intelligent plant 2024/04/05
- Topstar Special | National Science and Technology Workers Day 2024/04/05
HOT TOPIC
- 3 in 1 Compact Dehumidifying Dryer
- 5-axis CNC machine
- accuracy
- Air Chillers
- all electric injection molding machine
- all electric injection molding machines
- All-electric injection molding machines
- and overall production quality. Therefore
- AP-RubberPlas
- automated injection molding machine
- Automation changed engineering
- automation of injection molding robots
- auxiliary machine
- Bench Injection Molding Machine
- Cabinet dryer manufacturers
- Cabinet dryers
- chiller
- CNC Drilling Machine
- CNC Drilling Machines
- cnc engraving machine manufacturer
- cnc laser cutting machine manufacturer
- CNC machine
- CNC Machine Center
- CNC Machine for Sale
- CNC Machine Manufacturing
- CNC Machine Tool
- CNC machine tool product
- CNC Machining Center
- CNC wood carving machine
- Cooling system
- Cross-Walking Single Axis Servo Cylinder Robot
- Cross-Walking Single-Axis Servo Cylinder Robot
- Cross-Walking Three-Axis/Five-Axis Servo Driven Robot
- cross-walking three-axis/five-axis servo-driven robot
- Dehumidifier Dryer
- Dehumidifying Dryer
- delta parallel robot
- Desktop Injection Molding Machine
- Desktop injection molding machines
- Desktop Molding Machine
- desktop plastic injection machine
- Desktop Plastic Injection Molding Machine
- direct clamp injection molding machine
- Direct clamp injection molding machines
- Dosing & mixing system
- Drilling Centers
- Drying and dehumidification system
- drying and dehumidifying equipment
- Drying and Dehumidifying System
- drying system
- effective and efficient. Cabinet dryers are also used in other industries where large quantities of material need to be dried
- efficient injection molding machine
- elbow hydraulic injection molding machines
- electric injection molding machine
- electric injection molding machines
- energy-saving injection molding machine
- etc. Among injection molding robots
- exhibition
- features of CNC machine
- Feeding And Conveying System
- Five Axis Machine Center
- Fully automatic injection molding machine
- Gathering Topstar
- giant injection molding machine
- GMU-600 5-Axis Machining Center
- Granulating & Recycling System
- Heavy duty injection molding machine
- High-precision electric molding machines
- high-precision plastic molding machines
- Honeycomb rotor dehumidifier
- horizontal injection molding machine
- Horizontal Injection Molding Machines
- Horizontal Injection Moulding Machine
- Horizontal Mixer manufacturer
- How The CNC Machine Works
- hybrid injection molding machine
- hydraulic injection molding machine
- Hydraulic Injection Molding Machines
- in this article
- Industrial robot
- Industrial Robot Chinese brand
- industrial robot parts
- industrial robot supplier
- Industrial robots
- Industry Chain
- Injection Manipulator
- injection manipulator robot
- injection mold machines
- Injection molding
- Injection molding automation
- Injection Molding Automation Solution
- injection molding dryer
- Injection molding equipment
- injection molding hopper dryer
- Injection molding machine
- injection molding machine brand
- Injection Molding Machine Factory
- Injection Molding Machine Manufacture
- Injection molding machine manufacturer
- injection molding machine manufacturers
- Injection molding machine procurement
- injection molding machine robotic arm
- injection molding machine with a robot
- Injection molding machines
- injection molding material dehumidifying
- injection molding plant
- Injection Molding Robot
- injection molding robot arm
- Injection molding robot automation
- Injection molding robotic arm
- injection molding robots
- Injection Moulding Robots
- Injection Robot
- Injection robot arm
- Injection robot manufacturer
- Injection robot wholesale
- injection robots
- intelligent injection molding machines
- Introducing Injection Robot
- It is the best choice for drying large quantities of material at once. Cabinetmakers use these machines because they are fast
- large injection molding machine
- Learn what industrial automation and robotics is
- linear robot
- low speed sound-proof granulator
- machine plastic molding
- make sure to add some! Improvements (2) Keyphrase in introduction: Your keyphrase or its synonyms appear in the first paragraph of the copy
- manipulator machine
- manufacturing
- micro injection molding machine
- middle speed granulator
- Mini CNC machine manufacturers.
- Mold Temperature Control System
- mold temperature controller
- molding material Dehumidifying System
- mould temperature controller
- mould temperature controllers
- New electric injection molding machine
- nitrogen dryer manufacturer
- nitrogen dryer system manufacturer
- Oil type mold temperature controller
- open day
- Outbound links: No outbound links appear in this page. Add some! Images: No images appear on this page. Add some! Internal links: No internal links appear in this page
- PET Preform injection molding
- phone case maker machine
- phone case making machine
- plastic bottle making machine
- plastic bottle manufacturing
- plastic bucket making machine
- plastic bucket manufacturing
- Plastic chair making machine
- plastic forming equipment
- plastic hopper dryer
- plastic injection machine
- plastic injection machines
- plastic injection molding
- Plastic injection molding equipment
- Plastic injection molding machine
- Plastic Injection Molding Machines
- plastic injection robot
- Plastic Molding machine
- Plastic Molding Machines
- plastic molding press
- plastic phone case making machine
- plastic-molding machine
- powerful granulator
- Powerful Type Sound-Proof Granulator
- precision injection molding
- production of plastic seats
- Robot injection molding
- robot injection molding machine
- robot manufacturing companies
- Robotic arm for injection molding machine
- robotic injection molding machines
- robotics in injection molding
- SCARA robot
- SCARA robots
- Service-oriented manufacturing
- Servo Cylinder Robot
- servo driven robot
- Servo Driven Robots
- servo injection robots
- Servo-Driven Robot
- Setup of injection machine
- Silicone Injection Molding Machine
- six-axis industrial robot
- Stainless Hopper Dryer
- Stainless Hopper Dryers
- star club
- swing arm robot
- the choice between servo-driven robots and hydraulic robots will have a certain impact on efficiency
- the most popular injection molding machine
- the type of injection molding robot
- toggle clamp injection molding machine
- Toggle Hydraulic Injection Molding Machines
- toggle injection molding machine
- Top 10 brands of injection robots
- Topstar
- Topstar Engineering
- Topstar Industrial Robots
- Topstar injection molding intelligent
- Topstar Scara Robots
- Useful Injection molding machine
- Vertical machining centers
- volumetric type blender
- water chiller
- water chillers
- water distributor
- Water Type MoldTemperature Controller
- We often face choices when performing injection molding. We will choose the type of injection molding machine
- wholesale of injection molding machines
- x carve CNC