Common operating problems and solutions for several plastic injection machine
2024/02/20 By Topstar
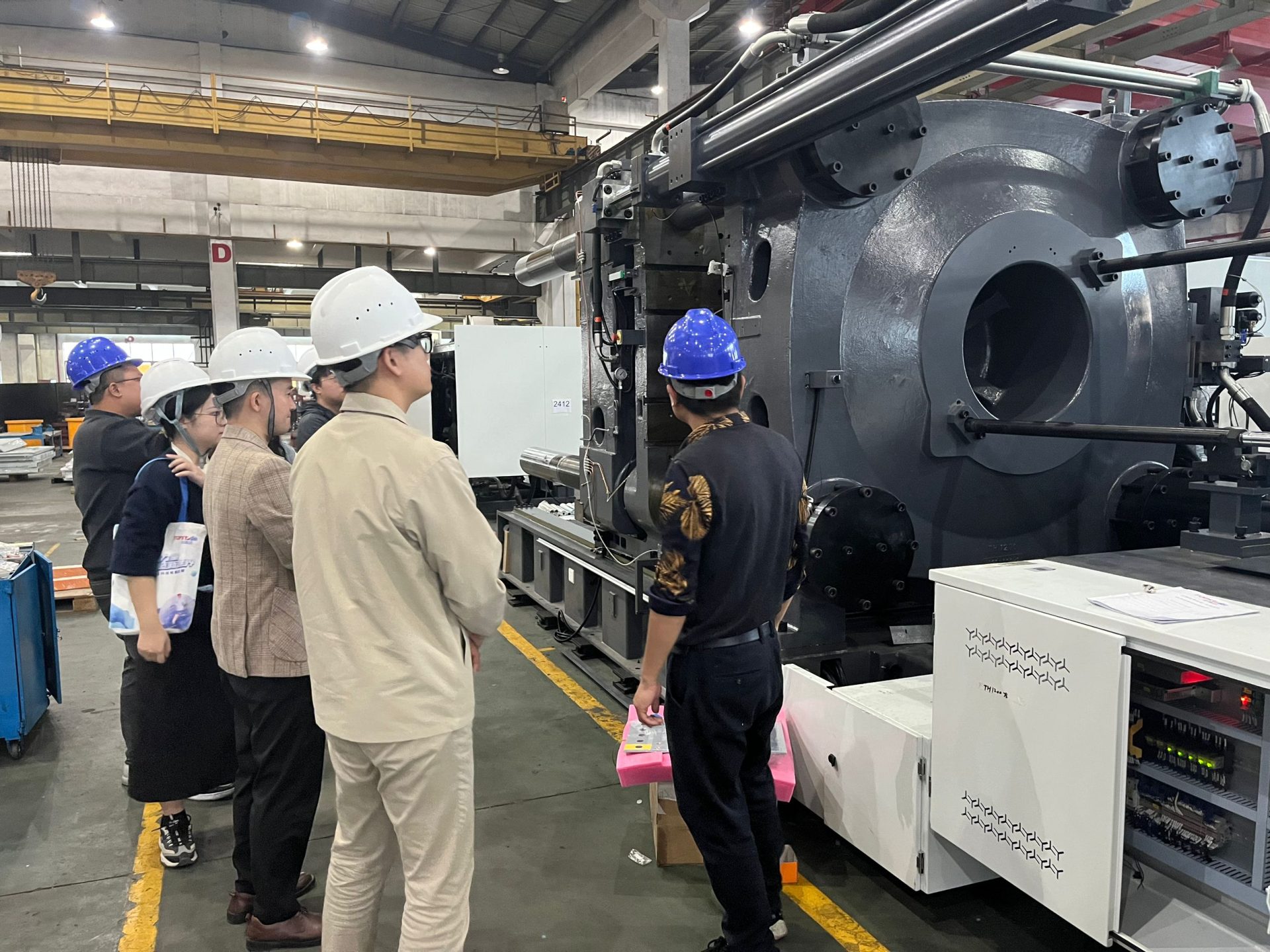
Plastic injection machine play a vital role in modern injection molding manufacturing processes. They are capable of producing a variety of plastic products. At the same time, operators will encounter many problems during their daily operations, and plastic injection machines are susceptible to various operational issues, disrupting production and affecting product quality. In this guide, we will give you some examples of standard operating problems encountered during the operation of injection molding machines and provide practical solutions to solve these problems.
Plastic injection machine nozzles and injection devices clogged
One of the common reasons plastic injection machines experience clogs in operation is the buildup of plastic residue or contaminants in the nozzle or injection device. This may result from inadequate cleaning procedures, poor-quality materials, or improper processing conditions. Regularly maintaining and cleaning injection equipment is crucial to solve this problem. Operators can clean the nozzles and injection devices using appropriate solvents or cleaners to remove accumulated residue and prevent clogs from forming.
Another possible reason is improper material selection or processing parameter settings. Using incompatible materials or not operating within the recommended temperature and pressure ranges can cause the injection molding material to degrade or overheat, causing the nozzle to clog. So, ensuring you’re using suitable materials and optimizing processing parameters for the specific material you’re processing can prevent clogging issues.
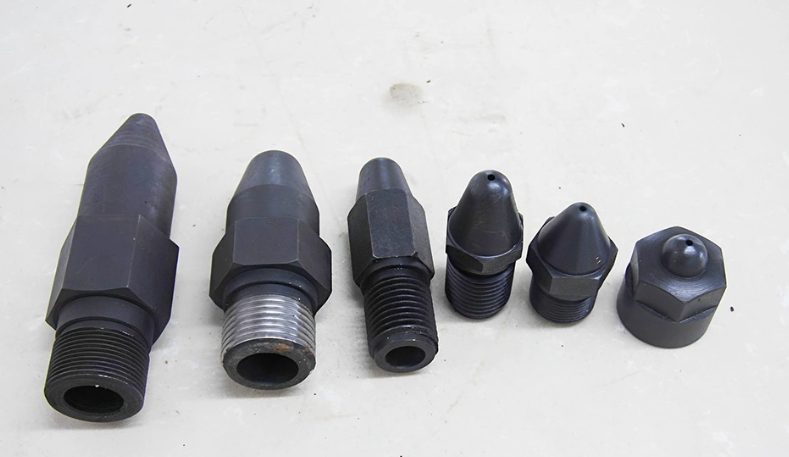
Plastic injection machine mold cooling issues
Common problems with plastic injection machine molds are insufficient cooling channel design or cooling capacity. Poor cooling can lead to uneven temperature distribution within the mold, resulting in longer cycle times, increased risk of defects, and reduced product part quality. To solve this problem, we optimize the design of cooling channels while increasing cooling capacity to improve heat dissipation and achieve a more uniform temperature distribution throughout the mold.
Also, improper placement or configuration of cooling channels can cause mold cooling issues. If cooling channels are poorly located or have inconsistent channel diameters or spacing, uneven cooling or hot spots may occur. These problems can be solved by adjusting the layout and configuration of the cooling channels to ensure even coverage and adequate cooling of the entire mold cavity.
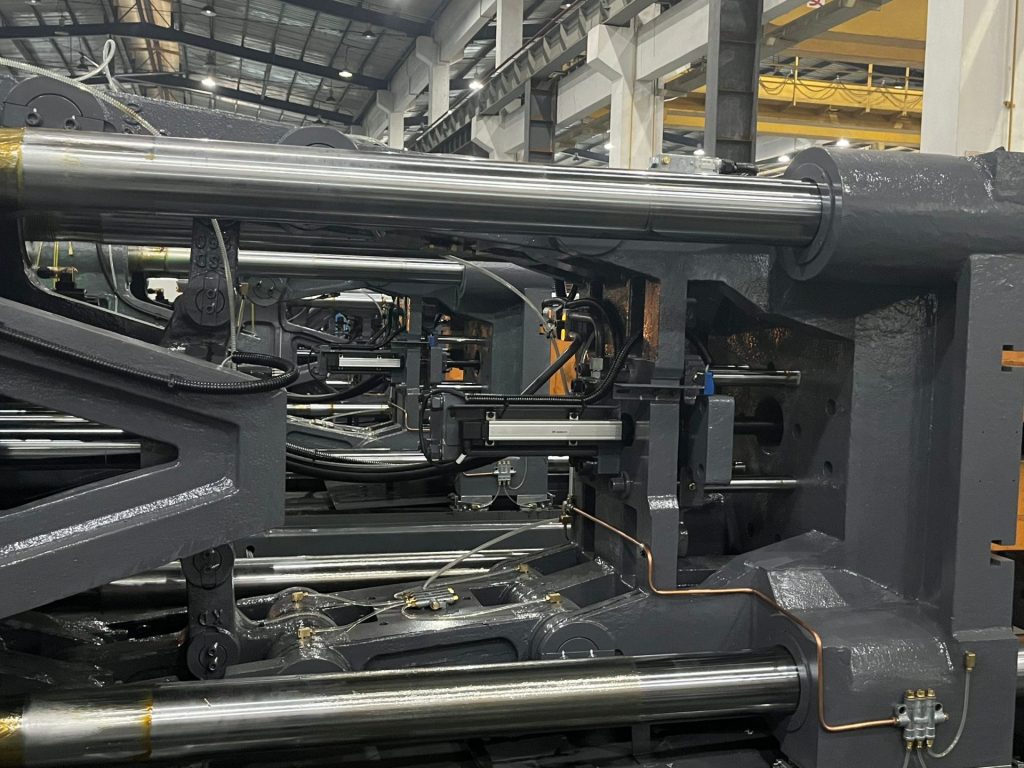
Injection pressure and temperature changes
One of the causes of unstable injection pressure in an injection molding machine is changes in material viscosity or melt flow behavior. Changes in material properties, such as temperature sensitivity or moisture content, can affect the material’s flow characteristics and cause fluctuations in injection pressure. Consistent material properties can be maintained by correctly storing and handling materials, monitoring material moisture content, and adjusting optimized processing parameters to address this issue.
In addition, the operator’s improper machine settings or operating conditions can also lead to unstable injection pressure. Suppose the injection pressure setting is not ideal. If the injection speed or pressure is too high, it can result in over- or under-packing of the mold cavity, resulting in part defects or inconsistencies. We then need to adjust the injection pressure settings to the optimal level based on material type, product shape, and mold design to reduce injection pressure variations.
plastic injection machine parts sticking and ejection problems
Plastic parts sticking is a common problem, and one of the contributing factors is insufficient or improper use of mold release agents. The proper release agent ensures even coverage, helps reduce sticking, and facilitates part removal. In addition, adhesion is minimized by optimizing mold surface finish and texture to reduce surface friction and promote easy release of molded parts. Ejection problems, such as incomplete or part deformation during ejection, will affect production efficiency and part quality. One of the common causes is insufficient ejection force or improper ejection pin design. We provide better support and prevent part deformation by increasing the ejection force or modifying the ejection pin shape.
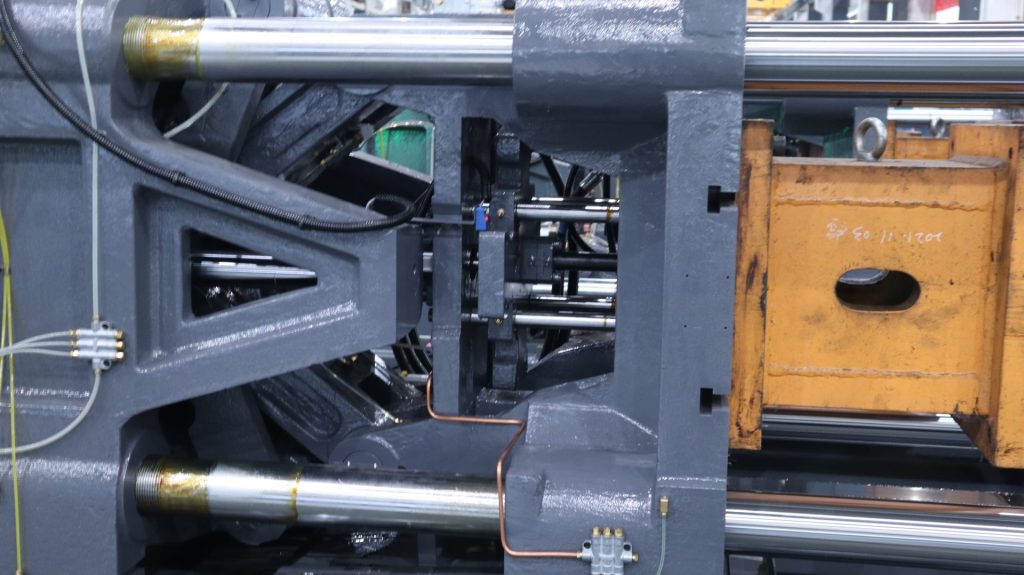
Machine failure due to hydraulic system problems
A common hydraulic system problem in plastic injection molding machines is oil leakage caused by worn seals, damaged hoses, or loose joints. To fix this problem, you must check the hydraulic system for signs of oil leakage, such as puddles or stains around hydraulic components. If damaged seals or hoses are found, tighten loose fittings and replace them promptly to prevent further leakage. Another hydraulic system problem is insufficient hydraulic pressure, which a failed pump, clogged valves, or contaminated fluid can cause. Identify deviations from standard operating pressure by checking hydraulic gauges and monitoring system performance. Periodically inspect hydraulic pumps, valves, and filters for wear or damage, and clean or replace components as needed to restore proper hydraulic pressure.
Electrical and control system failures
A typical electrical problem with plastic injection molding machines is power fluctuations or interruptions, which can disrupt machine operation and cause production delays. One can install protectors, voltage regulators, or uninterruptible power supply (UPS) systems to protect machines from voltage spikes, surges, or outages. Similar electrical wiring issues like loose connections, damaged wires, or short circuits can cause machine failure or shutdown. Operators must regularly inspect electrical wiring and connections, tighten open terminals, and replace damaged wires or connectors. In addition, control system failures can also affect machine performance and production quality. One must perform diagnostic testing using control system software or diagnostic tools to identify and resolve software or hardware-related issues.
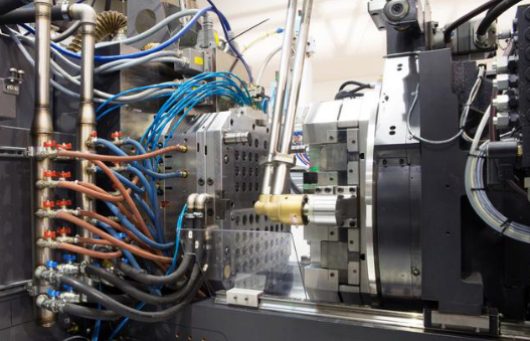
Improve plastic injection machine performance and reliability
Solving common operating problems of plastic injection machines is about improving their performance and reliability. In the article, we have listed several common issues and solutions. We hope users who read this guide can refer to our solutions to improve machine performance, reduce downtime, and improve product quality.
TRENDING POSTS
- What factors can cause delays in the injection molding process of plastic molding machine? 2024/02/20
- Exhibition Review| Topstar participates in InterPlas Thailand 2024 2024/02/20
- Star Case | Topstar helps Santong upgrade its intelligent plant 2024/02/20
- Topstar Special | National Science and Technology Workers Day 2024/02/20
HOT TOPIC
- 3 in 1 Compact Dehumidifying Dryer
- 5-axis CNC machine
- accuracy
- Air Chillers
- all electric injection molding machine
- All-electric injection molding machines
- and overall production quality. Therefore
- AP-RubberPlas
- automated injection molding machine
- Automation changed engineering
- automation of injection molding robots
- auxiliary machine
- Bench Injection Molding Machine
- Cabinet dryer manufacturers
- Cabinet dryers
- chiller
- CNC Drilling Machine
- CNC Drilling Machines
- cnc engraving machine manufacturer
- cnc laser cutting machine manufacturer
- CNC machine
- CNC Machine Center
- CNC Machine for Sale
- CNC Machine Manufacturing
- CNC Machine Tool
- CNC machine tool product
- CNC Machining Center
- CNC wood carving machine
- Cooling system
- Cross-Walking Single Axis Servo Cylinder Robot
- Cross-Walking Single-Axis Servo Cylinder Robot
- Cross-Walking Three-Axis/Five-Axis Servo Driven Robot
- cross-walking three-axis/five-axis servo-driven robot
- Dehumidifier Dryer
- Dehumidifying Dryer
- delta parallel robot
- Desktop Injection Molding Machine
- Desktop injection molding machines
- Desktop Molding Machine
- desktop plastic injection machine
- Desktop Plastic Injection Molding Machine
- direct clamp injection molding machine
- Direct clamp injection molding machines
- Dosing & mixing system
- Drilling Centers
- Drying and dehumidification system
- drying and dehumidifying equipment
- Drying and Dehumidifying System
- drying system
- effective and efficient. Cabinet dryers are also used in other industries where large quantities of material need to be dried
- efficient injection molding machine
- elbow hydraulic injection molding machines
- electric injection molding machine
- electric injection molding machines
- etc. Among injection molding robots
- exhibition
- features of CNC machine
- Feeding And Conveying System
- Five Axis Machine Center
- Fully automatic injection molding machine
- Gathering Topstar
- giant injection molding machine
- GMU-600 5-Axis Machining Center
- Granulating & Recycling System
- Heavy duty injection molding machine
- Honeycomb rotor dehumidifier
- horizontal injection molding machine
- Horizontal Injection Molding Machines
- Horizontal Injection Moulding Machine
- Horizontal Mixer manufacturer
- How The CNC Machine Works
- hybrid injection molding machine
- hydraulic injection molding machine
- Hydraulic Injection Molding Machines
- in this article
- Industrial robot
- Industrial Robot Chinese brand
- industrial robot parts
- industrial robot supplier
- Industrial robots
- Industry Chain
- Injection Manipulator
- injection mold machines
- Injection molding
- Injection molding automation
- Injection Molding Automation Solution
- injection molding dryer
- Injection molding equipment
- injection molding hopper dryer
- Injection molding machine
- injection molding machine brand
- Injection Molding Machine Factory
- Injection Molding Machine Manufacture
- Injection molding machine manufacturer
- injection molding machine manufacturers
- Injection molding machine procurement
- injection molding machine robotic arm
- injection molding machine with a robot
- Injection molding machines
- injection molding material dehumidifying
- injection molding plant
- Injection Molding Robot
- injection molding robot arm
- Injection molding robot automation
- Injection molding robotic arm
- injection molding robots
- Injection Moulding Robots
- Injection Robot
- Injection robot arm
- Injection robot manufacturer
- Injection robot wholesale
- injection robots
- intelligent injection molding machines
- Introducing Injection Robot
- It is the best choice for drying large quantities of material at once. Cabinetmakers use these machines because they are fast
- large injection molding machine
- Learn what industrial automation and robotics is
- low speed sound-proof granulator
- machine plastic molding
- make sure to add some! Improvements (2) Keyphrase in introduction: Your keyphrase or its synonyms appear in the first paragraph of the copy
- manipulator machine
- manufacturing
- micro injection molding machine
- middle speed granulator
- Mini CNC machine manufacturers.
- Mold Temperature Control System
- mold temperature controller
- molding material Dehumidifying System
- mould temperature controller
- mould temperature controllers
- New electric injection molding machine
- nitrogen dryer manufacturer
- nitrogen dryer system manufacturer
- Oil type mold temperature controller
- open day
- Outbound links: No outbound links appear in this page. Add some! Images: No images appear on this page. Add some! Internal links: No internal links appear in this page
- PET Preform injection molding
- phone case maker machine
- phone case making machine
- plastic bottle making machine
- plastic bottle manufacturing
- plastic bucket making machine
- plastic bucket manufacturing
- Plastic chair making machine
- plastic forming equipment
- plastic hopper dryer
- plastic injection machine
- plastic injection machines
- plastic injection molding
- Plastic injection molding equipment
- Plastic injection molding machine
- Plastic Injection Molding Machines
- plastic injection robot
- Plastic Molding machine
- Plastic Molding Machines
- plastic molding press
- plastic phone case making machine
- plastic-molding machine
- powerful granulator
- Powerful Type Sound-Proof Granulator
- production of plastic seats
- Robot injection molding
- robot injection molding machine
- robot manufacturing companies
- Robotic arm for injection molding machine
- robotic injection molding machines
- robotics in injection molding
- SCARA robot
- SCARA robots
- Service-oriented manufacturing
- Servo Cylinder Robot
- servo driven robot
- Servo Driven Robots
- servo injection robots
- Servo-Driven Robot
- Setup of injection machine
- Silicone Injection Molding Machine
- six-axis industrial robot
- Stainless Hopper Dryer
- Stainless Hopper Dryers
- star club
- swing arm robot
- the choice between servo-driven robots and hydraulic robots will have a certain impact on efficiency
- the most popular injection molding machine
- the type of injection molding robot
- toggle clamp injection molding machine
- Toggle Hydraulic Injection Molding Machines
- toggle injection molding machine
- Top 10 brands of injection robots
- Topstar
- Topstar Engineering
- Topstar Industrial Robots
- Topstar injection molding intelligent
- Topstar Scara Robots
- Useful Injection molding machine
- Vertical machining centers
- volumetric type blender
- water chiller
- water chillers
- water distributor
- Water Type MoldTemperature Controller
- We often face choices when performing injection molding. We will choose the type of injection molding machine
- wholesale of injection molding machines
- x carve CNC