The impact of Drying and Dehumidifying System on molded parts
2023/11/11 By Topstar
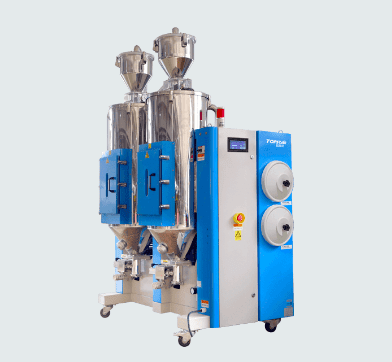
The surface finish of injection molded parts has always been critical. It determines whether it can be adapted to the corresponding product and affects our users’ views on corporate and industry standards. Drying and Dehumidifying System is ancillary to the entire injection molding process, and they have become a catalyst for achieving a harmonious synergy between form and function. In this article, we’ll take a closer look at the interplay between these systems and explore how they not only enhance structural integrity but also help improve the aesthetics of molded parts, providing customers with precise and smooth cuts with varying requirements.
Understand the role of moisture!
Manufacturers often mistakenly underestimate the pervasive effects of moisture, viewing it as an adversary in the complex world of injection molding. The potential presence of humidity in plastic resin fabrics can manifest as various defects, from seemingly inconspicuous minor blemishes to severe structural damage. Well-designed drying and dehumidifying Systems, equipped with advanced dehumidification mechanisms, actively tune into the nuances of potential pitfalls when dealing with this complex environment. This meticulous coordination ensures not only the prevention of defects but also the proactive advancement of surface quality to unprecedented levels of excellence.
By delving deeper into the subtle ways moisture affects material behavior, manufacturers can harness the full potential of these systems not only to ensure that defects are free but also to cultivate a surface finish that reflects the epitome of quality craftsmanship.
Precision and control of Drying and Dehumidifying System
Achieving a smooth surface finish is a complex process that relies heavily on the precision and control of drying and dehumidification systems. These systems enable manufacturers to finely calibrate moisture levels, creating consistent material behavior throughout the injection molding. It’s about making surfaces that exceed expectations. This subtlety of control represents a paradigm shift in how surface finishes are handled in the injection molding world, where mastery of moisture control transforms the manufacturing process into a creative endeavor.
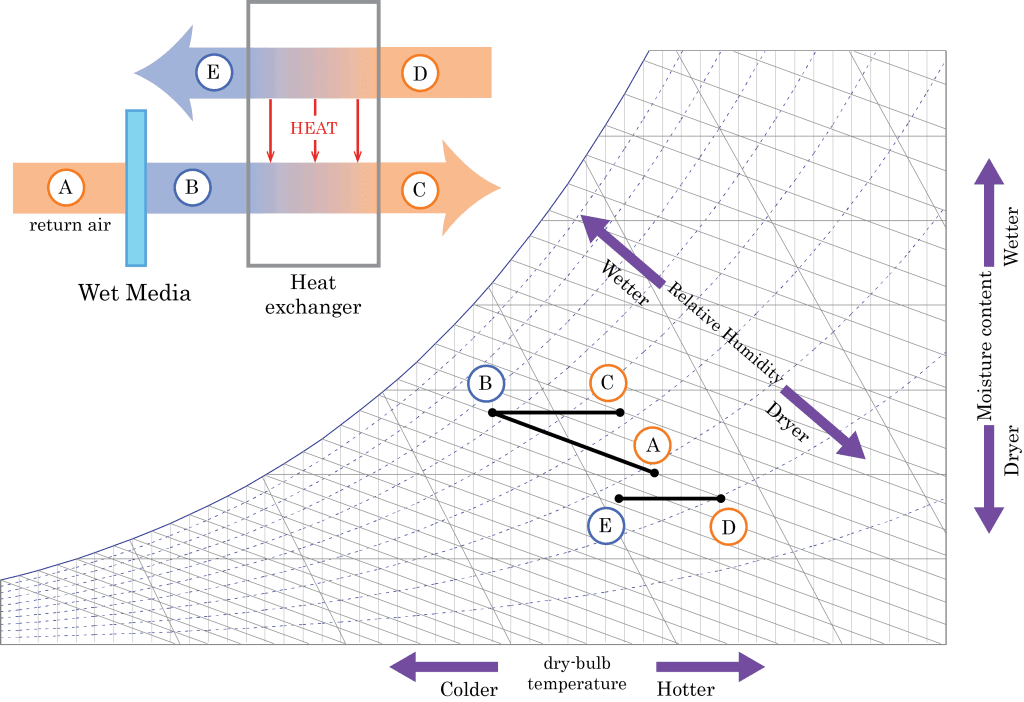
Effect of drying temperature on surface quality
The drying temperature is a seemingly simple parameter but is a critical variable in the delicate balance between effective moisture removal and maintaining surface quality. The effect of temperature on surface finish is not just a mechanical process but a symphony that requires careful orchestration. Achieving the proper temperature balance becomes an art form, ensuring the material does not compromise its structural integrity while drying. Each product is a testament to the mastery of temperature control in injection molding, with the right balance elevating the result to a level of aesthetic excellence.
Innovation in Desiccant Technology
Desiccant technology is a powerhouse in moisture control, with innovations that redefine the boundaries of achievable surface finish quality. The relentless pursuit of precision has resulted in capabilities once considered unbelievable. Advanced tools, including precise humidity control, rapid drying cycles, and self-adjusting mechanisms, elevate surface finish quality to unprecedented heights. As industries embrace these innovations, they not only future-proof their manufacturing processes but also open up new possibilities for creating products that demonstrate the seamless integration of cutting-edge technology and artistic skill.
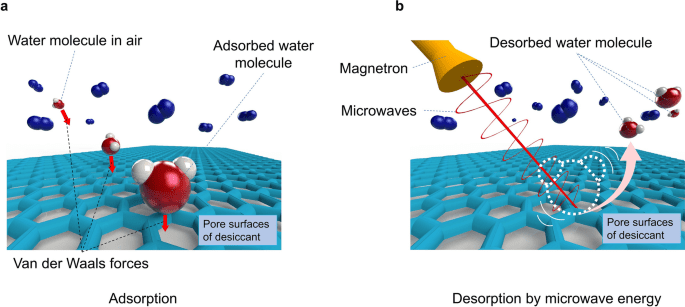
The role of Drying and Dehumidifying System in production environment
Creating pristine surfaces in a clean production environment is a meticulous and essential aspect of modern manufacturing. Drying and dehumidification systems in this process are vital as they help maintain the optimal conditions required to achieve impeccable surface quality. In a clean production environment, maintaining consistent surface properties is critical. Drying and dehumidification systems are vital in controlling environmental conditions, ensuring materials maintain their expected properties throughout production. Meticulous control ensures that products achieve surfaces that not only meet but often exceed the exacting standards set by an industry where precision cannot be compromised.
Take surface finish to unprecedented heights!
The relentless pursuit of perfection in form and function forces injection molding machine manufacturers to treat these systems as valuable components and indispensable partners in pursuing excellence. The industry expects that the trajectory of progress will be positive, promising breakthrough innovation. Businesses that adopt and expertly adapt to these cutting-edge systems meet and consistently exceed consumer expectations. The transformative impact of these systems goes beyond mere compliance to fundamentally improve the overall surface finish of molded parts to unprecedented levels, setting a new benchmark in manufacturing.
TRENDING POSTS
- What factors can cause delays in the injection molding process of plastic molding machine? 2023/11/11
- Exhibition Review| Topstar participates in InterPlas Thailand 2024 2023/11/11
- Star Case | Topstar helps Santong upgrade its intelligent plant 2023/11/11
- Topstar Special | National Science and Technology Workers Day 2023/11/11
HOT TOPIC
- .ervo motor-driven linear robots
- 1.0 guangdong topstar technology co. ltd
- 1.0 topstar china
- 1.0 topstar robot
- 11
- 2
- 21
- 23
- 3 axis robot
- 3 axis robots
- 3 in 1 Compact Dehumidifying Dryer
- 3-axis robot
- 3-axis robots
- 39
- 41
- 5-axis CNC machine
- 62
- accuracy
- Air Chillers
- all electric injection molding machine
- all electric injection molding machines
- All-electric injection molding machines
- and overall production quality. Therefore
- AP-RubberPlas
- automated injection molding machine
- Automation changed engineering
- automation of injection molding robots
- auxiliary machine
- Bench Injection Molding Machine
- Cabinet dryer manufacturers
- Cabinet dryers
- chiller
- CNC Drilling Machine
- CNC Drilling Machines
- cnc engraving machine manufacturer
- cnc laser cutting machine manufacturer
- CNC machine
- CNC Machine Center
- CNC Machine for Sale
- CNC Machine Manufacturing
- CNC Machine Tool
- CNC machine tool product
- CNC Machining Center
- CNC wood carving machine
- Cooling system
- Cross-Walking Single Axis Servo Cylinder Robot
- Cross-Walking Single-Axis Servo Cylinder Robot
- Cross-Walking Three-Axis/Five-Axis Servo Driven Robot
- cross-walking three-axis/five-axis servo-driven robot
- Dehumidifier Dryer
- Dehumidifying Dryer
- delta parallel robot
- Desktop Injection Molding Machine
- Desktop injection molding machines
- Desktop Molding Machine
- desktop plastic injection machine
- Desktop Plastic Injection Molding Machine
- direct clamp injection molding machine
- Direct clamp injection molding machines
- Dosing & mixing system
- Drilling Centers
- Drying and dehumidification system
- drying and dehumidifying equipment
- Drying and Dehumidifying System
- drying system
- effective and efficient. Cabinet dryers are also used in other industries where large quantities of material need to be dried
- efficient injection molding machine
- elbow hydraulic injection molding machines
- electric injection molding machine
- electric injection molding machines
- energy-efficient injection molding robot
- energy-saving injection molding machine
- etc. Among injection molding robots
- exhibition
- features of CNC machine
- Feeding And Conveying System
- Five Axis Machine Center
- Fully automatic injection molding machine
- Gathering Topstar
- giant injection molding machine
- GMU-600 5-Axis Machining Center
- Granulating & Recycling System
- Heavy duty injection molding machine
- High-precision electric molding machines
- high-precision plastic molding machines
- high-speed all electric injection molding machine
- Honeycomb rotor dehumidifier
- horizontal injection molding machine
- Horizontal Injection Molding Machines
- Horizontal Injection Moulding Machine
- Horizontal Mixer manufacturer
- How The CNC Machine Works
- hybrid injection molding machine
- hydraulic injection molding machine
- Hydraulic Injection Molding Machines
- in this article
- Industrial robot
- Industrial Robot Chinese brand
- industrial robot parts
- industrial robot supplier
- Industrial robots
- Industry Chain
- Injection Manipulator
- injection manipulator robot
- injection mold machines
- Injection molding
- Injection molding automation
- Injection Molding Automation Solution
- injection molding dryer
- Injection molding equipment
- injection molding hopper dryer
- Injection molding machine
- injection molding machine brand
- Injection Molding Machine Factory
- Injection Molding Machine Manufacture
- Injection molding machine manufacturer
- injection molding machine manufacturers
- Injection molding machine procurement
- injection molding machine robotic arm
- injection molding machine with a robot
- Injection molding machines
- injection molding material dehumidifying
- injection molding plant
- Injection Molding Robot
- injection molding robot arm
- Injection molding robot automation
- Injection molding robotic arm
- injection molding robots
- Injection moulding machine
- Injection Moulding Robots
- Injection Robot
- Injection robot arm
- Injection robot manufacturer
- Injection robot wholesale
- injection robots
- intelligent injection molding machines
- Introducing Injection Robot
- It is the best choice for drying large quantities of material at once. Cabinetmakers use these machines because they are fast
- large injection molding machine
- large injection molding machines
- Learn what industrial automation and robotics is
- linear robot
- linear robots
- low speed sound-proof granulator
- machine plastic molding
- make sure to add some! Improvements (2) Keyphrase in introduction: Your keyphrase or its synonyms appear in the first paragraph of the copy
- manipulator machine
- manufacturing
- medical grade injection molding machines
- medical injection molding machine
- medical injection molding machines
- micro injection molding machine
- middle speed granulator
- Mini CNC machine manufacturers.
- Mold Temperature Control System
- mold temperature controller
- mold temperature controllers
- molding material Dehumidifying System
- mould temperature control system
- mould temperature controller
- mould temperature controllers
- New electric injection molding machine
- nitrogen dryer manufacturer
- nitrogen dryer system manufacturer
- Oil type mold temperature controller
- Oil type mold temperature controllers
- open day
- Outbound links: No outbound links appear in this page. Add some! Images: No images appear on this page. Add some! Internal links: No internal links appear in this page
- PET Preform injection molding
- phone case maker machine
- phone case making machine
- plastic bottle making machine
- plastic bottle manufacturing
- plastic bucket making machine
- plastic bucket manufacturing
- Plastic chair making machine
- plastic forming equipment
- plastic hopper dryer
- plastic injection machine
- plastic injection machines
- plastic injection molding
- Plastic injection molding equipment
- Plastic injection molding machine
- Plastic Injection Molding Machines
- plastic injection moulding machine
- plastic injection robot
- Plastic Molding machine
- Plastic Molding Machines
- plastic molding press
- plastic moulding machine
- plastic phone case making machine
- plastic-molding machine
- powerful granulator
- Powerful Type Sound-Proof Granulator
- precision injection molding
- precision injection molding machines
- production of plastic seats
- pure water mould temperature controller
- Robot injection molding
- robot injection molding machine
- robot manufacturing companies
- Robotic arm for injection molding machine
- robotic injection molding machines
- robotics in injection molding
- SCARA robot
- SCARA robots
- Service-oriented manufacturing
- Servo Cylinder Robot
- servo driven robot
- Servo Driven Robots
- servo injection robots
- servo motor-driven linear robots
- servo-driven 3-axis robot
- Servo-Driven Robot
- Setup of injection machine
- Silicone Injection Molding Machine
- six-axis industrial robot
- Stainless Hopper Dryer
- Stainless Hopper Dryers
- star club
- swing arm robot
- take-out robots
- the choice between servo-driven robots and hydraulic robots will have a certain impact on efficiency
- the most popular injection molding machine
- the type of injection molding robot
- toggle clamp injection molding machine
- Toggle Hydraulic Injection Molding Machines
- toggle injection molding machine
- Top 10 brands of injection robots
- Topstar
- Topstar Engineering
- Topstar Industrial Robots
- Topstar injection molding intelligent
- Topstar Scara Robots
- Useful Injection molding machine
- Vertical machining centers
- volumetric type blender
- water chiller
- water chillers
- water distributor
- water type mold temperature controller
- Water Type MoldTemperature Controller
- Water-Type Mould Temperature Controllers
- We often face choices when performing injection molding. We will choose the type of injection molding machine
- wholesale of injection molding machines
- x carve CNC
- 热门查询 点击次数 展示 排名 topstar