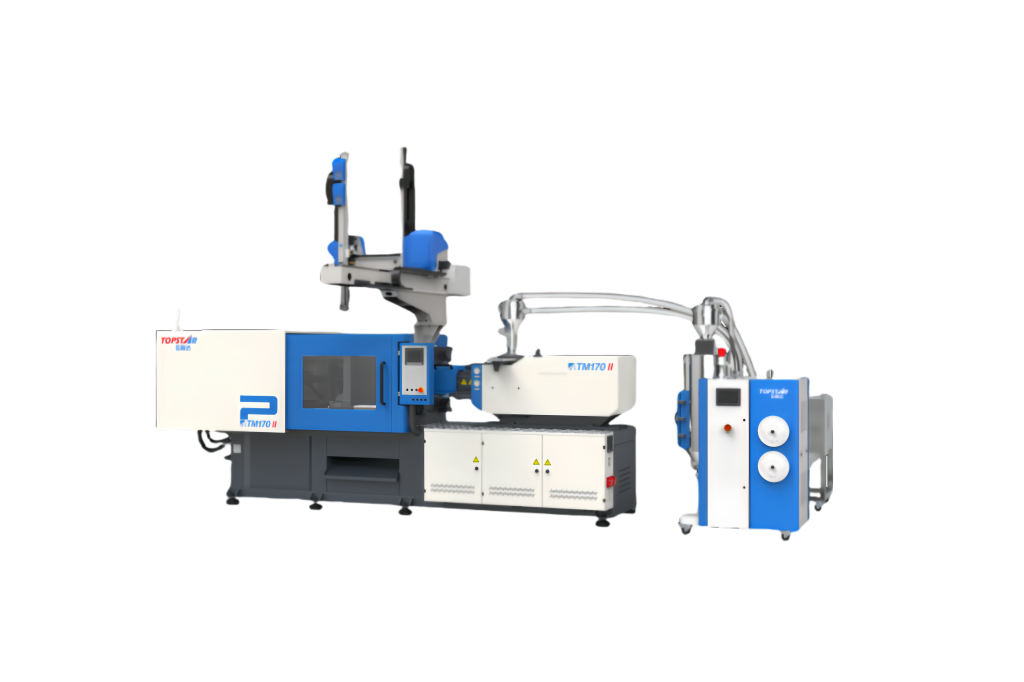
Plastic molding machine is at the heart of the modern injection molding process. They are used in various industries such as automotive, electronics, consumer goods, and packaging, and they can mass-produce high-precision plastic parts, making them an essential injection molding tool for plastic product production lines worldwide. As a manufacturer that provides injection molding solutions and produces injection molding machines, we will explore the six major features of plastic molding machines that will help you choose the equipment that is more suitable for your needs, whether you are in the automotive, medical, or packaging industry.
Key Features of Plastic Molding Machine: Precision and Accuracy
One of the most critical aspects of plastic molding machines is their precision and accuracy. The plastic molding machines provided by Topstar use an inclined double slide cylinder and linear guide design to make the injection more precise and stable, enabling it to produce parts with rich details and high consistency. The injection process itself is controlled by a combination of servo motors and a self-developed control system, ensuring that the material is injected into the mold cavity at a precise pressure, temperature, and speed. This precision reduces the margin of error in the final product, which is crucial for industries that require tight tolerances. Through precise molding, manufacturers can minimize rework and ensure that plastic parts fit perfectly during assembly. This precision is critical to industries that require high product reliability.
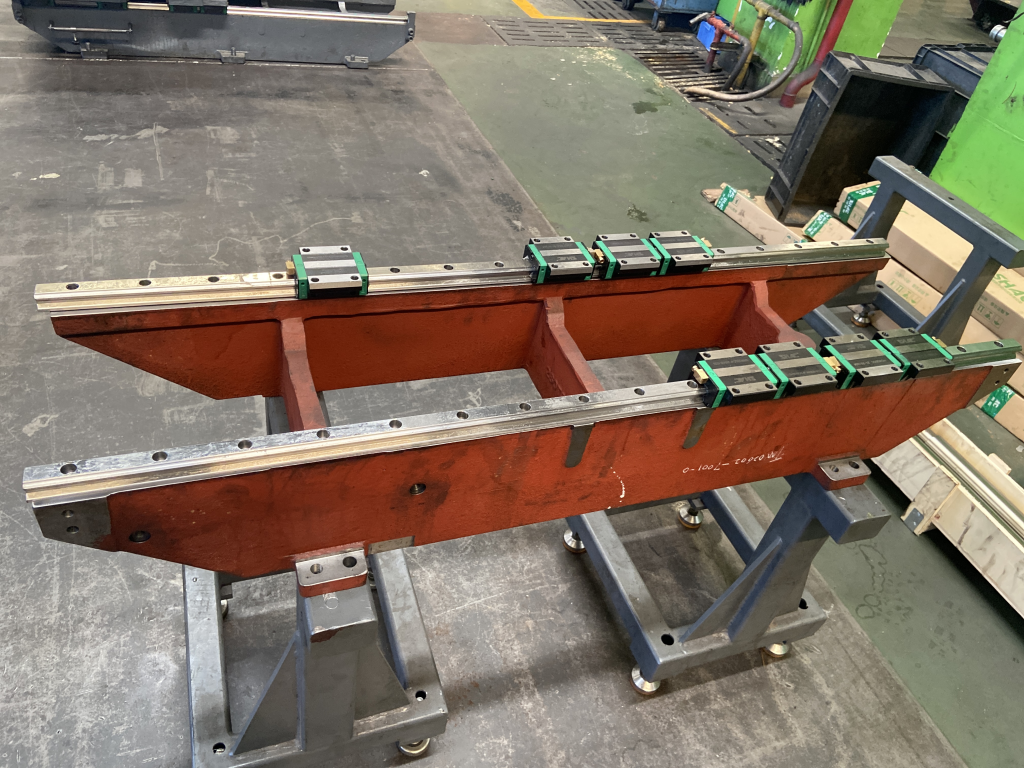
Energy Efficiency with Plastic Molding Machine
Energy efficiency is a concern for many customers today. Plastic molding machines, especially hydraulic ones, consume much energy, mainly when producing large parts. However, electric injection molding machines can significantly improve energy consumption. Topstar’s electric injection molding machines use energy-saving systems that significantly reduce the energy used in the molding process. They use servo-driven motors that adjust power consumption according to the needs of each part produced. While reducing energy consumption, servo-driven motors operate at very low and smooth speeds and eliminate product flow marks, bringing more sustainable operations and lower energy costs to manufacturers and ensuring the integrity of product quality.
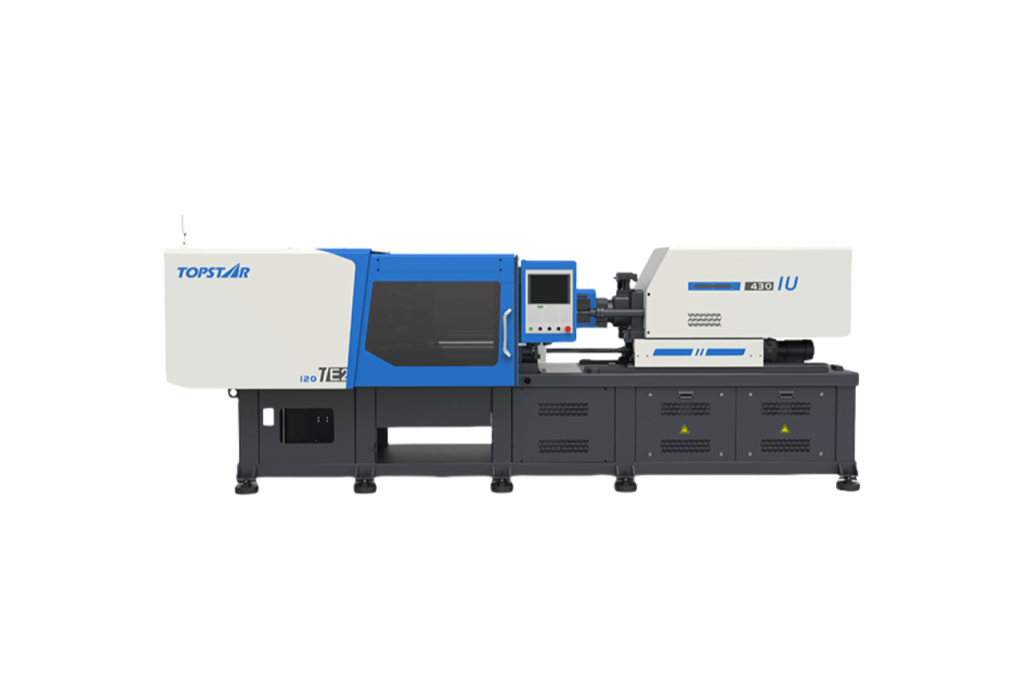
Production Versatility
Another outstanding feature of plastic molding machines is their versatility. The ability to manufacture various small complex parts to large structural parts makes them invaluable in many fields. Plastic molding machines produce simple consumer goods such as packaging and complex automotive parts, medical devices, and electronic components. With proper adjustments, plastic molding machines can be easily customized to produce a variety of plastic grades, shapes, and sizes. Topstar’s plastic molding machines can efficiently replace and accommodate different types of molds, including multi-cavity molds, through automatic one-button mold adjustment, ensuring that manufacturers can produce large quantities of the same part or complex components with multiple functions. This flexibility makes it an excellent choice for manufacturers in industries where product designs change rapidly.
Reduce cycle time and improve productivity
Cycle time is a key factor in determining the productivity and efficiency of any molding operation. With the continuous pursuit of higher output, reducing cycle time without sacrificing quality is an issue many customers value. Topstar’s plastic molding machines adopt the “injection molding process integration” design that can be integrated with surrounding injection molding equipment to provide faster cycle times, including faster injection speeds, improved mold cooling systems, and automated processes. The reduction in cycle time directly contributes to increased productivity. By increasing productivity, companies can meet higher demands without compromising the quality of parts. This feature is particularly beneficial for high-volume industries such as consumer products. In addition, adjusting cycle time according to the part’s complexity allows for more efficient resource management, optimizing the use of labor and energy.
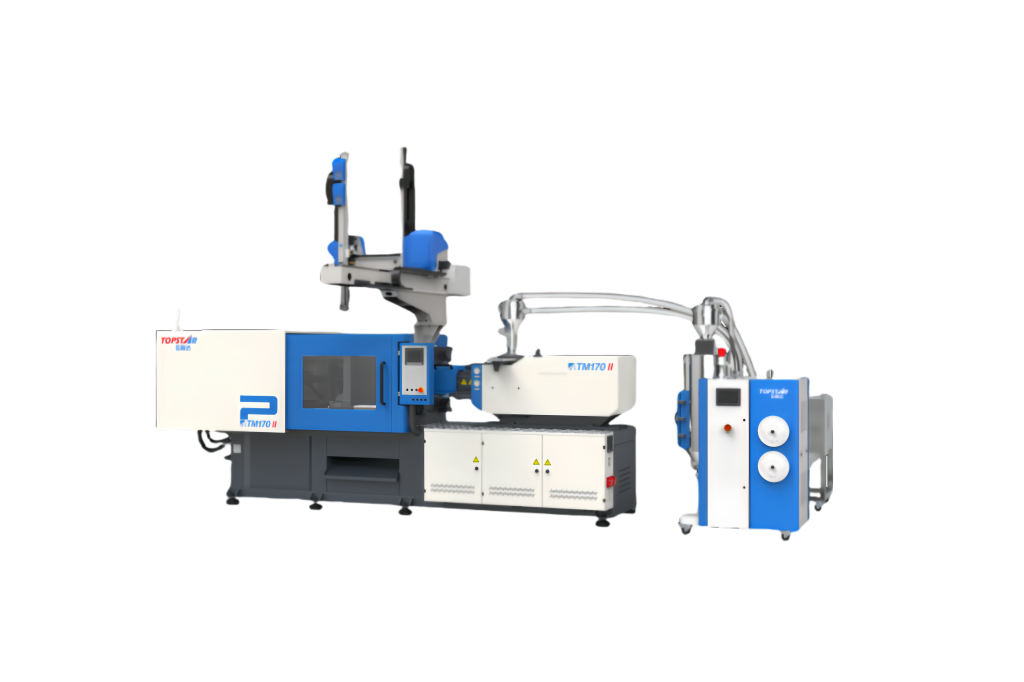
User-friendly interface
For complex machines, operators need straightforward and intuitive controls to ensure that they can operate the equipment effectively and safely. Topstar’s plastic molding machines have user-friendly interfaces that allow operators to monitor and control various machine functions easily. These interfaces include touchscreen controls, real-time injection pressure and temperature monitoring, and automatic troubleshooting. In addition, they all feature data analysis capabilities that provide real-time performance insights, allowing operators to identify potential problems before they cause production downtime quickly. With this sophisticated yet user-friendly system, operators can manage the machine’s performance with minimal training, thereby reducing human errors and improving overall efficiency.
Reliability and durability of plastic molding machines
Whether electric or hydraulic plastic molding machines, Topstar is manufactured with high-rigidity platens, complete stress analysis, and proper strength design. They have a wide range of template and mold support, stable dynamic support, smooth mold opening and closing, and better protection of molds and machines. They can provide consistent performance for many years, even under high-pressure conditions. In addition, with regular maintenance and care, the machine can maintain optimal performance, ensuring that production schedules are met without significant interruptions. The durability of components such as injection units and molds ensures that machine performance remains stable, reducing the need for expensive repairs or replacement parts. This high reliability means higher overall value for manufacturers.
Ultimately
Plastic molding machines’ precision and accuracy, energy efficiency, versatility, reduced cycle times, user-friendly interfaces, and reliability demonstrate their critical importance in achieving optimal production efficiency and product quality. Manufacturers can increase productivity, reduce costs, and meet customer expectations by choosing the right machine.
TRENDING POSTS
- What factors can cause delays in the injection molding process of plastic molding machine? 2021/12/24
- Exhibition Review| Topstar participates in InterPlas Thailand 2024 2021/12/24
- Star Case | Topstar helps Santong upgrade its intelligent plant 2021/12/24
- Topstar Special | National Science and Technology Workers Day 2021/12/24
HOT TOPIC
- 3 in 1 Compact Dehumidifying Dryer
- 5-axis CNC machine
- accuracy
- Air Chillers
- all electric injection molding machine
- All-electric injection molding machines
- and overall production quality. Therefore
- AP-RubberPlas
- automated injection molding machine
- Automation changed engineering
- automation of injection molding robots
- auxiliary machine
- Bench Injection Molding Machine
- Cabinet dryer manufacturers
- Cabinet dryers
- chiller
- CNC Drilling Machine
- CNC Drilling Machines
- cnc engraving machine manufacturer
- cnc laser cutting machine manufacturer
- CNC machine
- CNC Machine Center
- CNC Machine for Sale
- CNC Machine Manufacturing
- CNC Machine Tool
- CNC machine tool product
- CNC Machining Center
- CNC wood carving machine
- Cooling system
- Cross-Walking Single Axis Servo Cylinder Robot
- Cross-Walking Single-Axis Servo Cylinder Robot
- Cross-Walking Three-Axis/Five-Axis Servo Driven Robot
- cross-walking three-axis/five-axis servo-driven robot
- Dehumidifier Dryer
- Dehumidifying Dryer
- delta parallel robot
- Desktop Injection Molding Machine
- Desktop injection molding machines
- Desktop Molding Machine
- desktop plastic injection machine
- Desktop Plastic Injection Molding Machine
- direct clamp injection molding machine
- Direct clamp injection molding machines
- Dosing & mixing system
- Drilling Centers
- Drying and dehumidification system
- drying and dehumidifying equipment
- Drying and Dehumidifying System
- drying system
- effective and efficient. Cabinet dryers are also used in other industries where large quantities of material need to be dried
- efficient injection molding machine
- elbow hydraulic injection molding machines
- electric injection molding machine
- electric injection molding machines
- etc. Among injection molding robots
- exhibition
- features of CNC machine
- Feeding And Conveying System
- Five Axis Machine Center
- Fully automatic injection molding machine
- Gathering Topstar
- giant injection molding machine
- GMU-600 5-Axis Machining Center
- Granulating & Recycling System
- Heavy duty injection molding machine
- Honeycomb rotor dehumidifier
- horizontal injection molding machine
- Horizontal Injection Molding Machines
- Horizontal Injection Moulding Machine
- Horizontal Mixer manufacturer
- How The CNC Machine Works
- hybrid injection molding machine
- hydraulic injection molding machine
- Hydraulic Injection Molding Machines
- in this article
- Industrial robot
- Industrial Robot Chinese brand
- industrial robot parts
- industrial robot supplier
- Industrial robots
- Industry Chain
- Injection Manipulator
- injection mold machines
- Injection molding
- Injection molding automation
- Injection Molding Automation Solution
- injection molding dryer
- Injection molding equipment
- injection molding hopper dryer
- Injection molding machine
- injection molding machine brand
- Injection Molding Machine Factory
- Injection Molding Machine Manufacture
- Injection molding machine manufacturer
- injection molding machine manufacturers
- Injection molding machine procurement
- injection molding machine robotic arm
- injection molding machine with a robot
- Injection molding machines
- injection molding material dehumidifying
- injection molding plant
- Injection Molding Robot
- injection molding robot arm
- Injection molding robot automation
- Injection molding robotic arm
- injection molding robots
- Injection Moulding Robots
- Injection Robot
- Injection robot arm
- Injection robot manufacturer
- Injection robot wholesale
- injection robots
- intelligent injection molding machines
- Introducing Injection Robot
- It is the best choice for drying large quantities of material at once. Cabinetmakers use these machines because they are fast
- large injection molding machine
- Learn what industrial automation and robotics is
- low speed sound-proof granulator
- machine plastic molding
- make sure to add some! Improvements (2) Keyphrase in introduction: Your keyphrase or its synonyms appear in the first paragraph of the copy
- manipulator machine
- manufacturing
- micro injection molding machine
- middle speed granulator
- Mini CNC machine manufacturers.
- Mold Temperature Control System
- mold temperature controller
- molding material Dehumidifying System
- mould temperature controller
- mould temperature controllers
- New electric injection molding machine
- nitrogen dryer manufacturer
- nitrogen dryer system manufacturer
- Oil type mold temperature controller
- open day
- Outbound links: No outbound links appear in this page. Add some! Images: No images appear on this page. Add some! Internal links: No internal links appear in this page
- PET Preform injection molding
- phone case maker machine
- phone case making machine
- plastic bottle making machine
- plastic bottle manufacturing
- plastic bucket making machine
- plastic bucket manufacturing
- Plastic chair making machine
- plastic forming equipment
- plastic hopper dryer
- plastic injection machine
- plastic injection machines
- plastic injection molding
- Plastic injection molding equipment
- Plastic injection molding machine
- Plastic Injection Molding Machines
- plastic injection robot
- Plastic Molding machine
- Plastic Molding Machines
- plastic molding press
- plastic phone case making machine
- plastic-molding machine
- powerful granulator
- Powerful Type Sound-Proof Granulator
- production of plastic seats
- Robot injection molding
- robot injection molding machine
- robot manufacturing companies
- Robotic arm for injection molding machine
- robotic injection molding machines
- robotics in injection molding
- SCARA robot
- SCARA robots
- Service-oriented manufacturing
- Servo Cylinder Robot
- servo driven robot
- Servo Driven Robots
- servo injection robots
- Servo-Driven Robot
- Setup of injection machine
- Silicone Injection Molding Machine
- six-axis industrial robot
- Stainless Hopper Dryer
- Stainless Hopper Dryers
- star club
- swing arm robot
- the choice between servo-driven robots and hydraulic robots will have a certain impact on efficiency
- the most popular injection molding machine
- the type of injection molding robot
- toggle clamp injection molding machine
- Toggle Hydraulic Injection Molding Machines
- toggle injection molding machine
- Top 10 brands of injection robots
- Topstar
- Topstar Engineering
- Topstar Industrial Robots
- Topstar injection molding intelligent
- Topstar Scara Robots
- Useful Injection molding machine
- Vertical machining centers
- volumetric type blender
- water chiller
- water chillers
- water distributor
- Water Type MoldTemperature Controller
- We often face choices when performing injection molding. We will choose the type of injection molding machine
- wholesale of injection molding machines
- x carve CNC