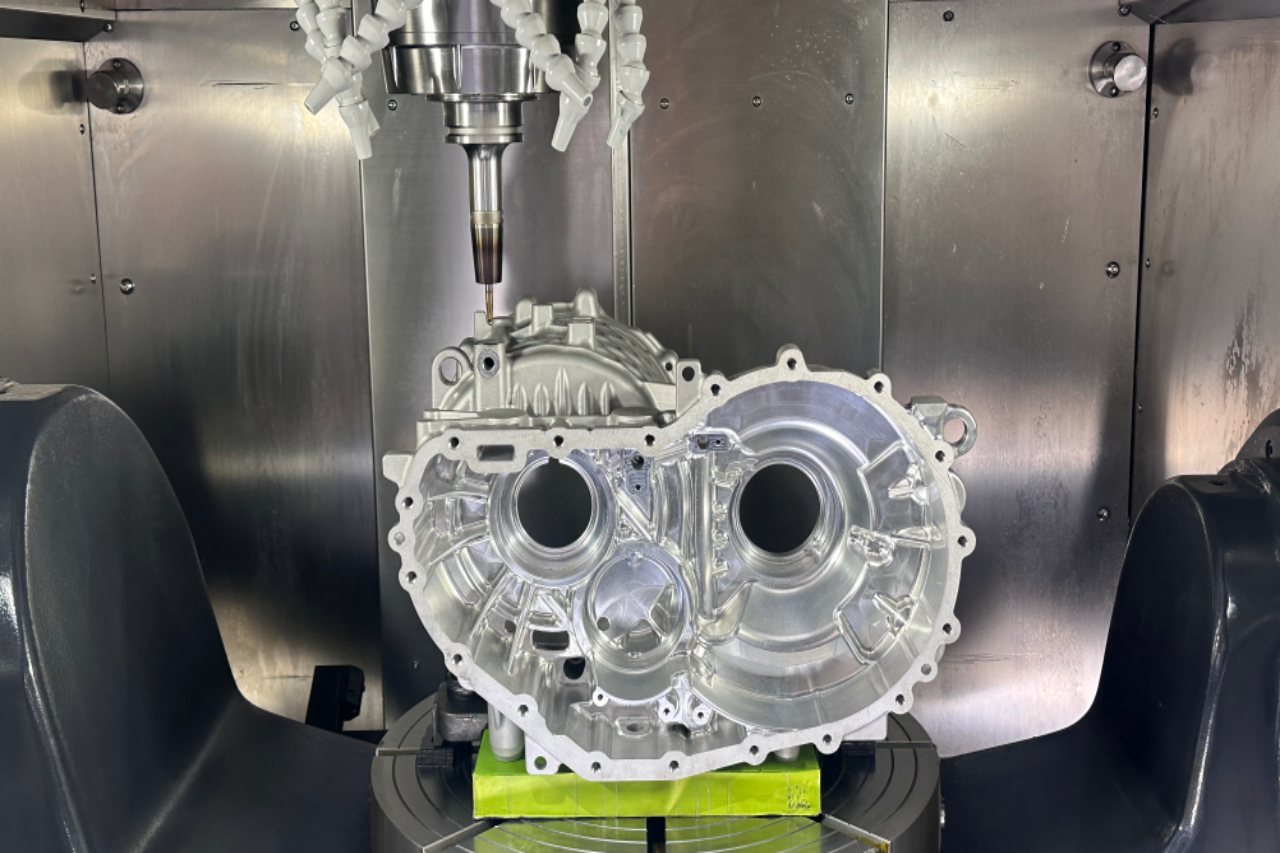
As one of the new global productivity representatives, the manufacturing process of new energy vehicles’ three core components (motor, battery, and electronic control) has put higher requirements for metal housing processing. The gearbox housing accommodates gears and bearings that transmit power and torque in the mechanical system and has high precision, rigidity, and stability requirements. For more manufacturing industries to cope with the challenges of high precision, high beat requirements, and complex contours in processing new energy vehicle parts, Topstar brings a 5-axis CNC machine-gearbox housing processing solution to meet industry production’s precision and lightweight requirements.
5-axis CNC machine meets high precision requirements
One of the biggest challenges in machining gearbox housings is to meet the high precision requirements of various components (including bearing holes, gear shafts, and mounting surfaces) and to ensure the accuracy of gearbox housing processing. The gearbox housing requires strict accuracy control to ensure the smooth operation of internal gears, bearings, and seals. 5-axis CNC machine can achieve high dynamic response and excellent rotation accuracy.
Among them, the C axis of the GMU-600 5-axis machining center is directly driven by a DD motor with a speed of 80 rpm, providing excellent dynamic response and rotational accuracy, which can achieve exact positioning. By using a direct drive motor, excellent angular positioning accuracy can be achieved. This ensures the machining process achieves the highest precision, the gearbox housing meets strict quality standards, and reliable, high-performance components are produced.
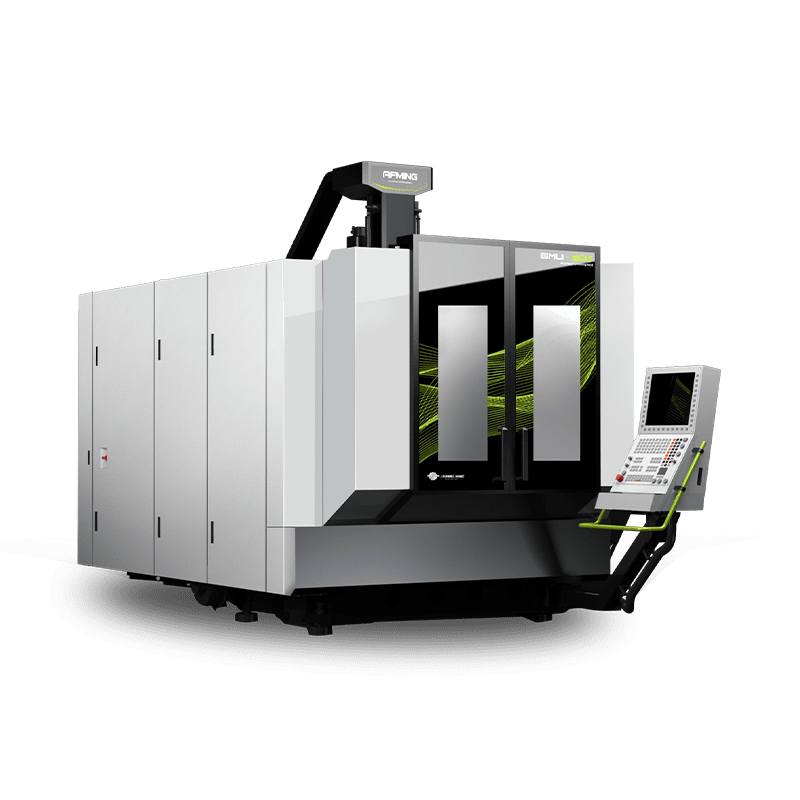
5-axis CNC machine meets high cycle requirements
Many gearbox manufacturers must produce parts in large quantities, so they must use Machining Centers that simultaneously handle high throughput and excellent precision. The GMU-600 5-axis machining center optimizes the machining process and is ideal for mass production of gearbox housings.
The design of the GMU-600 reduces non-productive time by improving the efficiency of each machining cycle.
Complex contours and thin-walled parts
Gearbox housings often have complex geometries, including contours, cavities, and thin-walled sections prone to vibration during machining. The 5-axis CNC machines uniquely equip themselves to meet these challenges easily.
The GMU-600 5-axis machining center uses a high-rigidity bed structure, precision transmission system design, and fine-cutting parameters—the three work together to minimize vibration and maintain stability during machining. The system can precisely control the cutting force to ensure that thin-walled parts are machined without compromising their structural integrity. In addition, the 5-axis CNC machine’s ability to move the tool in multiple directions simultaneously means that it can reach areas that are difficult or impossible to reach with traditional machine tools. This ability is critical for machining the complex contours familiar in gearbox housings, allowing manufacturers to achieve complex geometries with high precision.
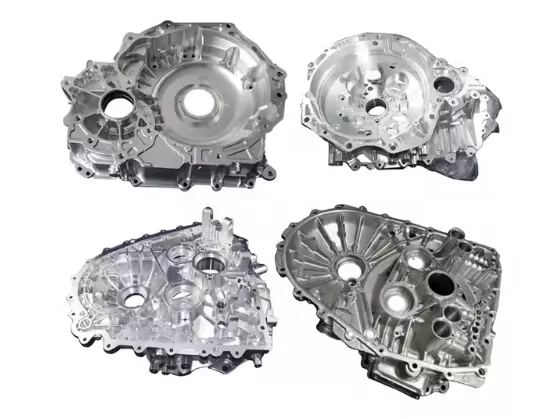
High concentricity requirements for bearing holes
The design team must ensure that the bearing holes in gearbox housings meet stringent concentricity requirements to align the gears and bearings properly during operation. The GMU-600’s A-axis has a DIN5 grade high-precision gear drive, providing 3500Nm of static torque. This high-precision gear drive allows accurate and consistent bearing bore machining with excellent concentricity. The ability of a 5-axis machining center to provide this high-precision machining capability helps improve the overall performance and life of the gearbox. In addition, the GMU-600’s advanced control system machines the bearing bore to a concentricity tolerance of 0.01 mm, which is critical to ensure that the bearings fit perfectly and run smoothly.
5-axis capabilities enhance machining flexibility
One of the main advantages of 5-axis CNC machine technology is its enhanced flexibility during machining. Conventional 3-axis machines limit their ability to reach certain areas of a part, especially when dealing with complex geometries or deep cavities. On the other hand, a 5-axis CNC machine can move the cutting tool in multiple directions simultaneously, enabling it to reach nearly any surface of the gearbox housing with greater precision and efficiency.
The GMU-600’s 5-axis capabilities enable manufacturers to machine parts with a single setup, reducing the need for multiple tool changes and setups. This simplifies the machining process, saving time and money while improving overall part consistency. This feature is very useful for achieving the complex geometries required by modern designs.
5-axis CNC machine enable high-precision machining of gearbox housings
Regarding machining gearbox housings, automotive, aerospace, and industrial manufacturers prefer 5-axis CNC machines due to their high accuracy, ability to handle complex geometries, and features that reduce vibration and ensure concentricity.
TRENDING POSTS
- What factors can cause delays in the injection molding process of plastic molding machine? 2024/12/20
- Exhibition Review| Topstar participates in InterPlas Thailand 2024 2024/12/20
- Star Case | Topstar helps Santong upgrade its intelligent plant 2024/12/20
- Topstar Special | National Science and Technology Workers Day 2024/12/20
HOT TOPIC
- .ervo motor-driven linear robots
- 3 axis robot
- 3 axis robots
- 3 in 1 Compact Dehumidifying Dryer
- 3-axis robot
- 3-axis robots
- 5-axis CNC machine
- accuracy
- Air Chillers
- all electric injection molding machine
- all electric injection molding machines
- All-electric injection molding machines
- and overall production quality. Therefore
- AP-RubberPlas
- automated injection molding machine
- Automation changed engineering
- automation of injection molding robots
- auxiliary machine
- Bench Injection Molding Machine
- Cabinet dryer manufacturers
- Cabinet dryers
- chiller
- CNC Drilling Machine
- CNC Drilling Machines
- cnc engraving machine manufacturer
- cnc laser cutting machine manufacturer
- CNC machine
- CNC Machine Center
- CNC Machine for Sale
- CNC Machine Manufacturing
- CNC Machine Tool
- CNC machine tool product
- CNC Machining Center
- CNC wood carving machine
- Cooling system
- Cross-Walking Single Axis Servo Cylinder Robot
- Cross-Walking Single-Axis Servo Cylinder Robot
- Cross-Walking Three-Axis/Five-Axis Servo Driven Robot
- cross-walking three-axis/five-axis servo-driven robot
- Dehumidifier Dryer
- Dehumidifying Dryer
- delta parallel robot
- Desktop Injection Molding Machine
- Desktop injection molding machines
- Desktop Molding Machine
- desktop plastic injection machine
- Desktop Plastic Injection Molding Machine
- direct clamp injection molding machine
- Direct clamp injection molding machines
- Dosing & mixing system
- Drilling Centers
- Drying and dehumidification system
- drying and dehumidifying equipment
- Drying and Dehumidifying System
- drying system
- effective and efficient. Cabinet dryers are also used in other industries where large quantities of material need to be dried
- efficient injection molding machine
- elbow hydraulic injection molding machines
- electric injection molding machine
- electric injection molding machines
- energy-efficient injection molding robot
- energy-saving injection molding machine
- etc. Among injection molding robots
- exhibition
- features of CNC machine
- Feeding And Conveying System
- Five Axis Machine Center
- Fully automatic injection molding machine
- Gathering Topstar
- giant injection molding machine
- GMU-600 5-Axis Machining Center
- Granulating & Recycling System
- Heavy duty injection molding machine
- High-precision electric molding machines
- high-precision plastic molding machines
- high-speed all electric injection molding machine
- Honeycomb rotor dehumidifier
- horizontal injection molding machine
- Horizontal Injection Molding Machines
- Horizontal Injection Moulding Machine
- Horizontal Mixer manufacturer
- How The CNC Machine Works
- hybrid injection molding machine
- hydraulic injection molding machine
- Hydraulic Injection Molding Machines
- in this article
- Industrial robot
- Industrial Robot Chinese brand
- industrial robot parts
- industrial robot supplier
- Industrial robots
- Industry Chain
- Injection Manipulator
- injection manipulator robot
- injection mold machines
- Injection molding
- Injection molding automation
- Injection Molding Automation Solution
- injection molding dryer
- Injection molding equipment
- injection molding hopper dryer
- Injection molding machine
- injection molding machine brand
- Injection Molding Machine Factory
- Injection Molding Machine Manufacture
- Injection molding machine manufacturer
- injection molding machine manufacturers
- Injection molding machine procurement
- injection molding machine robotic arm
- injection molding machine with a robot
- Injection molding machines
- injection molding material dehumidifying
- injection molding plant
- Injection Molding Robot
- injection molding robot arm
- Injection molding robot automation
- Injection molding robotic arm
- injection molding robots
- Injection moulding machine
- Injection Moulding Robots
- Injection Robot
- Injection robot arm
- Injection robot manufacturer
- Injection robot wholesale
- injection robots
- intelligent injection molding machines
- Introducing Injection Robot
- It is the best choice for drying large quantities of material at once. Cabinetmakers use these machines because they are fast
- large injection molding machine
- large injection molding machines
- Learn what industrial automation and robotics is
- linear robot
- linear robots
- low speed sound-proof granulator
- machine plastic molding
- make sure to add some! Improvements (2) Keyphrase in introduction: Your keyphrase or its synonyms appear in the first paragraph of the copy
- manipulator machine
- manufacturing
- medical grade injection molding machines
- medical injection molding machine
- medical injection molding machines
- micro injection molding machine
- middle speed granulator
- Mini CNC machine manufacturers.
- Mold Temperature Control System
- mold temperature controller
- mold temperature controllers
- molding material Dehumidifying System
- mould temperature control system
- mould temperature controller
- mould temperature controllers
- New electric injection molding machine
- nitrogen dryer manufacturer
- nitrogen dryer system manufacturer
- Oil type mold temperature controller
- Oil type mold temperature controllers
- open day
- Outbound links: No outbound links appear in this page. Add some! Images: No images appear on this page. Add some! Internal links: No internal links appear in this page
- PET Preform injection molding
- phone case maker machine
- phone case making machine
- plastic bottle making machine
- plastic bottle manufacturing
- plastic bucket making machine
- plastic bucket manufacturing
- Plastic chair making machine
- plastic forming equipment
- plastic hopper dryer
- plastic injection machine
- plastic injection machines
- plastic injection molding
- Plastic injection molding equipment
- Plastic injection molding machine
- Plastic Injection Molding Machines
- plastic injection moulding machine
- plastic injection robot
- Plastic Molding machine
- Plastic Molding Machines
- plastic molding press
- plastic moulding machine
- plastic phone case making machine
- plastic-molding machine
- powerful granulator
- Powerful Type Sound-Proof Granulator
- precision injection molding
- precision injection molding machines
- production of plastic seats
- pure water mould temperature controller
- Robot injection molding
- robot injection molding machine
- robot manufacturing companies
- Robotic arm for injection molding machine
- robotic injection molding machines
- robotics in injection molding
- SCARA robot
- SCARA robots
- Service-oriented manufacturing
- Servo Cylinder Robot
- servo driven robot
- Servo Driven Robots
- servo injection robots
- servo motor-driven linear robots
- servo-driven 3-axis robot
- Servo-Driven Robot
- Setup of injection machine
- Silicone Injection Molding Machine
- six-axis industrial robot
- Stainless Hopper Dryer
- Stainless Hopper Dryers
- star club
- swing arm robot
- take-out robots
- the choice between servo-driven robots and hydraulic robots will have a certain impact on efficiency
- the most popular injection molding machine
- the type of injection molding robot
- toggle clamp injection molding machine
- Toggle Hydraulic Injection Molding Machines
- toggle injection molding machine
- Top 10 brands of injection robots
- Topstar
- Topstar Engineering
- Topstar Industrial Robots
- Topstar injection molding intelligent
- Topstar Scara Robots
- Useful Injection molding machine
- Vertical machining centers
- volumetric type blender
- water chiller
- water chillers
- water distributor
- water type mold temperature controller
- Water Type MoldTemperature Controller
- Water-Type Mould Temperature Controllers
- We often face choices when performing injection molding. We will choose the type of injection molding machine
- wholesale of injection molding machines
- x carve CNC